shed shelving plans
Thursday, November 21, 2024
How to Build a Basic Shed for Your Outdoor Storage Needs

Building Your Dream Shed: A Step-by-Step Guide
Hey there, fellow DIY enthusiasts! So, you're thinking about building a shed? Fantastic! It's a really rewarding project, and the sense of accomplishment when it's finally finished is amazing. Plus, you'll have a fantastic space for all that garden clutter, your tools, or even a little workshop. This guide will walk you through building a basic shed, perfect for beginners. Don't worry, we'll keep it simple and straightforward.Planning and Preparation: The Foundation of Success
Before you even think about picking up a hammer, some serious planning is needed. This isn't just about measuring twice and cutting once (although that's important too!), it's about making sure everything is legally sound and you've got a solid plan to work from.Choosing Your Shed Location
Where will your shed live? This is a crucial decision. Consider:- Accessibility: Do you need easy access from your house or garage?
- Sunlight: Do you want a sunny spot, or would shade be better?
- Ground conditions: Is the ground level and stable? You might need to do some leveling.
- Local regulations: Check with your local council about building permits, setbacks (how far from your property line you can build), and any other restrictions.
Designing Your Shed: Size and Materials
How big do you need your shed to be? This depends entirely on what you plan to store in it. Think about the dimensions carefully. A smaller shed is easier and cheaper to build, but a bigger one will obviously offer more storage space. When choosing materials, pressure-treated lumber is a great option for the frame because it's resistant to rot and insects. For the cladding (the outer covering), you could use anything from more pressure-treated wood to metal or even plastic sheeting â" it really depends on your budget and aesthetic preferences. I recommend sketching out a rough design, noting all the dimensions.Laying the Foundation: A Solid Start
A sturdy foundation is vital for a long-lasting shed. There are a few options:Concrete Slab Foundation
This is the most robust option, but also the most expensive and time-consuming. It involves pouring a concrete slab according to your shed's dimensions. This is a job best left to professionals unless you have experience with concrete work.Gravel Base Foundation
This is a more budget-friendly and simpler alternative. It involves excavating the area, laying down a layer of gravel (compacted thoroughly!), and then adding a layer of paving slabs or concrete pavers on top. This method works well for lighter sheds.Pier and Beam Foundation
This method involves setting concrete piers in the ground at each corner and along the sides of your shed. Wooden beams are then placed on top of the piers to create a framework for your shed floor. This is a good compromise between cost and sturdiness.Building the Frame: The Shed's Skeleton
Once your foundation is set, it's time to construct the frame. This is where accurate measurements and careful cutting become crucial.Cutting and Assembling the Walls
Using your pre-cut lumber, assemble the wall frames, making sure all corners are square and secure. Use appropriate screws and connectors to create strong joints. It might be helpful to build the walls flat on the ground for easier assembly.Erecting the Walls
Carefully lift and position your assembled walls onto the foundation. You might need an extra pair of hands for this part! Ensure they are plumb (perfectly vertical) and use temporary supports to keep them in place until they are secured to the base plates.Building the Roof Frame
The roof frame is typically constructed separately, either as a gable roof (with a triangular shape) or a shed roof (with a single slope). Again, precise measurements are key. Youâll need to cut rafters (for a gable roof) or roof joists (for a shed roof) to the correct angles and lengths.Attaching the Roof to the Walls
Once the roof frame is complete, carefully lift it onto the walls and secure it firmly in place.Cladding and Finishing Touches: Bringing Your Shed to Life
With the frame complete, it's time to add the finishing touches.Adding the Cladding
This is where your chosen cladding material comes into play. Whether youâre using wood, metal, or plastic, follow the manufacturerâs instructions for installation. Pay attention to overlapping the sheets to ensure waterproofing.Adding Doors and Windows
Install your doors and windows, ensuring they are properly sealed to prevent drafts and leaks.Finishing Touches
Consider adding a floor, painting or staining the exterior, adding a lock for security, and installing shelving inside.Commonly Asked Questions
Q: Do I need a building permit? A: This depends on your local regulations. It's always best to check with your local council before starting any construction project.
Q: How long does it take to build a shed? A: The time it takes varies greatly depending on the size and complexity of your shed, as well as your experience. A simple shed could take a weekend, while a more complex one might take several weekends.
Q: What tools do I need? A: Youâll need basic carpentry tools like a hammer, saw, screwdriver, measuring tape, level, and drill. More specialized tools might be necessary depending on your chosen materials and design.
Q: How much does it cost to build a shed? A: The cost varies significantly based on size, materials, and the type of foundation you choose. Expect to spend anywhere from a few hundred to several thousand dollars.
Q: Can I build a shed by myself? A: While itâs possible, itâs often easier and safer to have a helper, especially for lifting heavy materials. If you lack experience, consider seeking help from a more experienced DIYer or even hiring a professional for certain aspects of the project.
Remember, building a shed is a journey, not a race. Take your time, enjoy the process, and you'll end up with a fantastic outdoor storage solution you can be proud of! Happy building!How to Build a Wood Pallet Shed: Simple, Practical, and Budget-Friendly
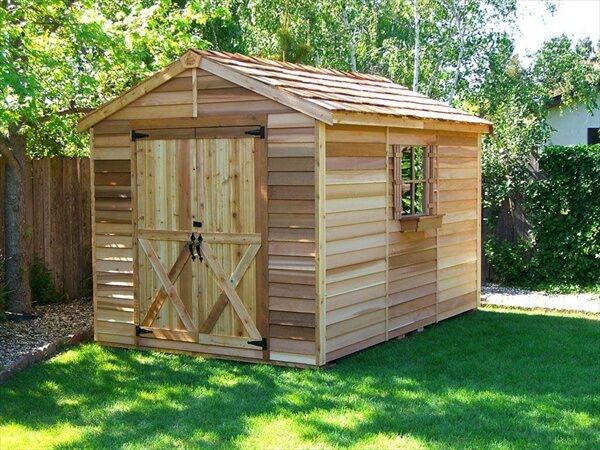
Constructing a Budget-Friendly Wood Pallet Shed: A Comprehensive Guide
The desire for additional storage space is a common theme among homeowners and property owners alike. Traditional shed construction can prove costly and time-consuming. However, a resourceful and practical alternative exists: constructing a shed from reclaimed wood pallets. This guide provides a detailed, step-by-step approach to building a functional and aesthetically pleasing pallet shed, minimizing costs while maximizing practicality.
I. Planning and Preparation: Laying the Foundation for Success
Before commencing construction, meticulous planning is paramount. This phase ensures the project proceeds smoothly and yields a structurally sound and aesthetically pleasing result. Careful consideration must be given to several key aspects:
A. Shed Design and Dimensions
The dimensions of your pallet shed will be dictated primarily by the available space and your storage needs. Sketching a basic design, including the overall dimensions (length, width, and height), door placement, and window placement (if desired), is a crucial first step. Consider the number and size of pallets required to achieve your desired dimensions. Remember to factor in the thickness of the pallet wood when calculating the final dimensions. Standard pallet sizes are readily available, making them convenient for planning.
B. Site Selection and Ground Preparation
Selecting an appropriate site is critical for both structural integrity and ease of access. Choose a level area with good drainage to prevent water accumulation and potential damage to the shed. Clear the area of any debris, vegetation, or obstructions. For a more permanent structure, consider preparing a concrete slab foundation. For a simpler, temporary structure, a compacted gravel base will suffice. The chosen base will significantly impact the longevity and stability of the shed.
C. Material Acquisition and Assessment
The core material for this project is reclaimed wood pallets. Inspect each pallet thoroughly for signs of rot, pest infestation, or significant damage. Select only pallets in good condition, ensuring they are structurally sound for use in construction. You may need to source pallets from multiple locations, and the quality may vary. It's advisable to acquire more pallets than initially anticipated to account for potential damage or unusable sections. Supplemental materials, including nails, screws, wood sealant, and paint (optional) should also be gathered.
II. Construction Phase: Assembling the Pallet Shed
Once the preparatory phase is complete, the construction process can begin. This involves several distinct stages, each requiring careful attention to detail:
A. Base Construction
Constructing a sturdy base is crucial for the structural integrity of the entire shed. If using a concrete slab, ensure it's level and properly cured before proceeding. For a gravel base, compact the gravel thoroughly to provide a stable foundation. The initial layer of pallets will serve as the shed's floor. Secure them to the base using appropriate fasteners, ensuring a level and stable surface. For improved stability and water resistance, consider adding a layer of plywood or pressure-treated lumber on top of the pallet floor.
B. Wall Construction
The pallet walls are constructed by stacking pallets vertically. Ensure the pallets are aligned and properly secured using nails or screws. Use multiple fasteners per pallet to enhance structural rigidity. Consider reinforcing the corners with additional bracing using sturdy lumber. A plumb bob or level can be used to ensure the walls remain vertical and plumb throughout the construction process. For additional stability, consider using metal corner brackets to strengthen the joints.
C. Roof Construction
The roof design can vary depending on preference and available materials. A simple gable roof is relatively easy to construct. Begin by creating the roof trusses using sturdy lumber and connecting them securely to the top of the walls. The pallets can then be used to create the roof decking, laying them horizontally across the trusses and securing them with nails or screws. Ensure proper overlap to prevent water leakage. Consider adding roofing felt or another waterproof membrane before finishing the roof to further enhance protection against the elements.
D. Door and Window Installation (Optional)
The incorporation of a door and windows significantly enhances the shedâs functionality and aesthetics. If constructing a door from pallets, use sturdy pallets and reinforce the frame. Use appropriate hinges and a latch or lock for security. Windows can be created using pallet sections or purchased pre-made windows. Seal all gaps and openings to prevent drafts and moisture ingress.
III. Finishing Touches: Enhancing Durability and Aesthetics
The final phase involves enhancing the shed's durability, weather resistance, and aesthetic appeal.
A. Sealing and Weatherproofing
Applying a wood sealant or protective coating is vital to safeguard the wood pallets from moisture damage, insect infestation, and weathering. This will significantly extend the lifespan of the shed. Select a high-quality sealant designed for outdoor use. Multiple coats may be necessary for optimal protection. Consider a waterproof membrane beneath the roofing material for added protection against leaks.
B. Painting or Staining (Optional)
Painting or staining the shed not only enhances its aesthetic appeal but can also provide additional protection against the elements. Select a weather-resistant paint or stain suitable for exterior use. Consider applying multiple coats for better durability and color consistency. Choose a color that complements the surrounding environment.
C. Interior Finishing (Optional)
Once the exterior is completed, consider adding interior features to enhance functionality. This might include shelves, hooks for hanging tools, or a workbench. These additions will increase the shed's usability and make it more efficient for storage.
IV. Safety Considerations
Throughout the construction process, prioritize safety. Wear appropriate safety gear, including safety glasses, gloves, and sturdy work boots. Use caution when handling tools and materials. Ensure the work area is well-lit and free of obstructions. Always follow the manufacturerâs instructions for any tools or materials used.
Building a wood pallet shed is a rewarding project that combines practicality, affordability, and environmental consciousness. By following this comprehensive guide and prioritizing meticulous planning and attention to detail, you can successfully construct a durable, functional, and visually appealing storage solution for your property.
Wednesday, November 20, 2024
Free Pallet Shed Plans PDF: Build a Functional and Stylish Shed
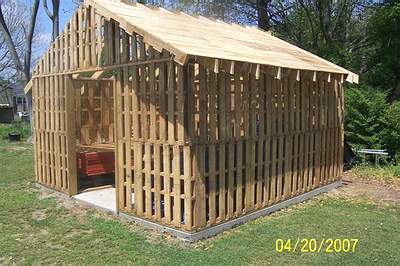
Free Pallet Shed Plans PDF: Build a Functional and Stylish Shed
This comprehensive guide provides detailed instructions and free downloadable PDF plans for constructing a functional and aesthetically pleasing shed utilizing reclaimed pallets. This project offers a cost-effective and environmentally conscious alternative to traditional shed construction, allowing for customization and creative expression.
Assessing Your Needs and Site Preparation
Before embarking on the construction of your pallet shed, careful planning is paramount. This initial phase involves several crucial steps that will directly impact the success and longevity of your project.
Determining Shed Dimensions and Functionality
The dimensions of your shed should be carefully considered based on its intended purpose. Consider the items you plan to store and ensure sufficient space for easy access and maneuverability. Common considerations include the storage of gardening equipment, tools, bicycles, or seasonal items. Sketching a preliminary design, noting the dimensions of your intended storage items, is a highly recommended practice. This will allow you to optimize the internal space and prevent unforeseen spatial constraints.
Site Selection and Ground Preparation
Selecting a suitable location for your shed is critical. Choose a level area with adequate sunlight and drainage. Avoid areas prone to flooding or excessive shade. The ground should be properly leveled and compacted to provide a stable foundation for your shed. Consider the proximity to power sources and water if you plan to incorporate electrical outlets or plumbing. Check local building codes and zoning regulations to ensure compliance with any relevant restrictions.
Material Acquisition and Pallet Assessment
Sourcing your pallets is a crucial step in this cost-effective project. Inspect pallets carefully for structural integrity; damaged or rotten wood is unsuitable. Ensure the pallets are treated for outdoor use. You will likely need a significant number of pallets, so plan your acquisition strategy accordingly. Consider contacting local businesses that frequently receive shipments on pallets, as they may be willing to donate or sell their used pallets at a discounted price.
Constructing the Pallet Shed Frame
The foundation of your pallet shed is its frame. The structural integrity of this frame will directly impact the longevity and stability of your completed shed. This section outlines the critical steps in constructing a robust and durable frame.
Foundation Construction
A solid foundation is essential for a stable shed. You have several options, including a concrete slab, a gravel base, or pressure-treated wooden sleepers. The chosen method will depend on your budget and the ground conditions. A leveled base is crucial, and ensuring proper drainage is imperative to prevent water damage.
Framing the Walls
Using your chosen pallets, begin constructing the walls. Ensure the pallets are securely fastened together using appropriate screws or nails. You may need to disassemble some pallets to achieve the desired dimensions and create openings for doors and windows. Remember to maintain consistent spacing and alignment throughout the construction process for a visually appealing and structurally sound shed.
Erecting the Frame
Once the walls are assembled, carefully erect the frame. This is best achieved with the assistance of another person to ensure stability and prevent accidents. Use temporary bracing to secure the frame until the roof is installed. Ensure the frame is plumb and square using a level and measuring tape. Any imperfections at this stage will significantly impact the final structure.
Roofing and Finishing Touches
The roof and finishing touches significantly enhance both the functionality and aesthetic appeal of your pallet shed. Consider the weather conditions in your area when selecting roofing materials.
Roofing Material Selection and Installation
Several roofing materials are compatible with a pallet shed, including corrugated metal sheeting, asphalt shingles, or even recycled plastic sheeting. Select a material that offers adequate protection from the elements and matches your aesthetic preferences. Ensure proper ventilation to prevent moisture buildup under the roof. Proper installation is crucial to guarantee watertight protection.
Door and Window Installation
Install doors and windows to provide access and natural light. You may use pre-fabricated doors and windows or construct your own from additional pallets and other materials. Ensure that the doors and windows are securely fastened and weatherproofed to prevent drafts and water damage.
Exterior and Interior Finishing
Enhance the durability and aesthetics of your shed through exterior and interior finishing. Consider sealing the wood with a weather-resistant sealant or paint to protect it from moisture and insects. Painting the interior walls can improve the overall appearance and potentially enhance the light reflection within the shed. Add shelving or other organizational features to maximize the storage space.
Safety Precautions and Legal Considerations
Safety is paramount throughout the entire construction process. Adherence to safety guidelines and legal requirements is critical to prevent accidents and ensure compliance.
Safety Gear and Procedures
Always wear appropriate safety gear, including safety glasses, gloves, and sturdy work boots. Use caution when handling power tools and sharp objects. Lift heavy items correctly to prevent back injuries. Follow the manufacturer's instructions for all tools and materials.
Building Permits and Local Regulations
Check with your local authorities regarding building permits and zoning regulations. Some jurisdictions require permits for shed construction, even for smaller structures. Failure to obtain necessary permits may result in fines or legal repercussions. Understand and comply with all local building codes to ensure your shed meets the required safety and structural standards.
Downloading the Free Pallet Shed Plans PDF
The detailed plans for constructing your pallet shed, including diagrams and specifications, are available for free download as a PDF document. [Insert Link to PDF Here]. These plans provide a comprehensive guide to assist you throughout the construction process. Remember to carefully review the plans before starting your project and adapt them to your specific needs and available resources.
Building a pallet shed is a rewarding project that combines functionality, sustainability, and creativity. By following these guidelines and utilizing the provided free PDF plans, you can create a valuable addition to your property that enhances both its aesthetic appeal and practical utility. Remember that careful planning, attention to detail, and adherence to safety standards are essential for a successful project outcome.
Saturday, November 16, 2024
Budget-Friendly 12x20 Shed Plans with Loft for Garden Storage

Budget-Friendly 12x20 Shed Plans with Loft for Garden Storage
This document provides comprehensive plans for constructing a budget-friendly 12x20 shed incorporating a loft for maximized storage capacity. The design prioritizes cost-effectiveness while maintaining structural integrity and functionality, ideal for gardeners needing ample space for tools, equipment, and seasonal items. The detailed plans encompass material lists, construction procedures, and considerations for minimizing expenses throughout the building process.
I. Design Specifications and Considerations
The proposed 12x20 shed design emphasizes practicality and affordability. The dimensions allow for substantial storage space on the ground floor and in the loft area. The inclusion of a loft significantly increases storage capacity without a proportional increase in the footprint of the shed. This design minimizes material waste and simplifies construction. The design can be adapted to suit individual needs and available materials. However, adhering to the specified dimensions and construction techniques will ensure optimal structural integrity and cost-effectiveness.
A. Overall Dimensions and Layout
The shedâs overall dimensions are 12 feet wide by 20 feet long. This allows for ample space for storage on the ground floor and generous headroom in the loft area. The ground floor area will be dedicated to larger equipment and tools, while the loft will be ideal for storing less frequently used items, such as seasonal decorations or excess gardening supplies. The internal layout should allow for easy navigation and efficient access to stored items.
B. Foundation Considerations
A cost-effective foundation solution for this shed is a concrete slab. This provides a solid and level base for the structure, preventing settling and rot. Alternatively, a gravel base with pressure-treated lumber framing can be used as a more economical option, particularly if the ground is well-drained. However, the concrete slab offers superior durability and protection against moisture.
C. Framing and Structure
The shed frame will utilize pressure-treated lumber for durability and resistance to rot and insect infestation. The framing will consist of 4x4 posts for the corners and 2x4 studs for the walls and roof. Standard construction techniques will be employed to ensure structural integrity. The use of readily available lumber sizes minimizes material costs and simplifies construction.
D. Roofing System
A gable roof design is recommended for this shed due to its simplicity and effectiveness in shedding water. This design also allows for the creation of a usable loft space. The roof will be constructed using standard roofing materials such as asphalt shingles or metal roofing. The choice of roofing material will depend on budget and aesthetic preferences, with asphalt shingles generally offering a more economical option.
E. Loft Access and Design
Access to the loft will be via a fixed staircase or a pull-down ladder, depending on budget and space considerations. A fixed staircase offers greater convenience but requires more space and materials. A pull-down ladder is a more cost-effective solution and occupies less floor space. The loft floor will be constructed using plywood or OSB sheathing, providing a sturdy and level surface for storage.
II. Materials List and Cost Estimation
The following is an estimated materials list. Prices will vary depending on location and supplier. It is crucial to obtain accurate pricing from local suppliers before commencing construction. This list serves as a guide and may need adjustments based on individual preferences and local availability.
A. Lumber
- Pressure-treated 4x4 posts: 8
- Pressure-treated 2x4 studs: Approximately 150 linear feet
- Plywood or OSB sheathing for walls and roof: Quantities will vary depending on wall and roof dimensions.
- Plywood or OSB for loft floor: Calculated based on loft dimensions.
- Trim boards: For finishing and aesthetic details
B. Roofing Materials
- Asphalt shingles or metal roofing: Quantity will depend on roof dimensions.
- Roofing felt or underlayment
- Roofing nails or screws
C. Foundation Materials
- Concrete (if using a concrete slab) or gravel (if using a gravel base)
- Rebar (if using a concrete slab)
- Pressure-treated lumber for framing (if using a gravel base)
D. Other Materials
- Exterior siding (e.g., vinyl, wood, metal): Chosen based on budget and aesthetic preferences
- Windows and doors: Size and quantity will depend on design preferences
- Fasteners (nails, screws, bolts)
- Exterior paint or stain
- Ladder or staircase materials (depending on loft access chosen)
Note: This is a partial list. A more detailed and precise materials list should be generated based on finalized design plans and specific supplier quotes.
III. Construction Process
The construction process will follow standard shed-building procedures. Attention to detail and adherence to building codes are essential. Detailed step-by-step instructions are beyond the scope of this document but are readily available from numerous online resources and books. Seeking assistance from experienced builders is recommended, especially for those lacking construction experience.
A. Foundation Preparation
This involves leveling the ground and preparing the chosen foundation (concrete slab or gravel base). The foundation should be sufficiently strong and level to support the shedâs weight.
B. Frame Construction
This involves assembling the walls and roof frame using pressure-treated lumber. Proper framing techniques are crucial for structural stability. Squareness and plumbness should be carefully checked throughout the construction process.
C. Sheathing and Roofing
This involves installing the plywood or OSB sheathing on the walls and roof, followed by the chosen roofing material. Proper installation techniques are crucial for weatherproofing and structural integrity.
D. Loft Construction
This involves building the loft floor using plywood or OSB sheathing, supported by appropriate framing. Ensure sufficient headroom and safe access to the loft area.
E. Siding and Finishing
This involves installing the chosen exterior siding, windows, and doors, followed by finishing touches such as painting or staining. Proper sealing and weatherproofing are crucial for long-term durability.
IV. Cost-Saving Strategies
Several strategies can be employed to minimize construction costs:
- Source materials from economical suppliers: Compare prices from various lumber yards and home improvement stores.
- Utilize reclaimed or salvaged materials where possible: This can significantly reduce material costs.
- Perform as much of the labor yourself as possible: This eliminates labor costs, although it requires time and skills.
- Prioritize simple designs: Avoid complex designs that require specialized materials or techniques.
- Consider DIY alternatives for some features: For instance, building your own staircase or using a simpler roofing system.
- Plan ahead and purchase materials in bulk: This can often result in significant savings.
By carefully planning and executing the construction process, a functional and aesthetically pleasing 12x20 shed with a loft can be built at a significantly reduced cost. Remember to always prioritize safety and adhere to local building codes.
Monday, November 11, 2024
How to Design a Pole Barn with Multiple Rooms for Storage

Alright, so you're thinking about building a pole barn. Great choice! They're super versatile, and with a little planning, you can turn it into a multi-room storage powerhouse.
Let's start with the basics:
First things first, let's talk about the size. How much stuff do you need to store? Do you need space for a workshop, a gardening area, or maybe a play area for the kids? Once you have an idea of the square footage you need, you can start to think about the layout.
Think like a puzzle:
Imagine your pole barn as a big blank canvas. You'll need to divide this space into different rooms, each with its own purpose. Do you want separate areas for tools, equipment, garden supplies, or maybe even a small office space?
Here's a typical layout to consider:
Main Storage Area: This is your core space. Think of it as the main living room of your pole barn. It's where you'll store the bulk of your stuff, like lawnmowers, bikes, and other seasonal items.
Workshop: If you're handy, a dedicated workshop is a must. You can set up your workbench, tools, and have plenty of room to work on projects.
Gardening Area: If you have a green thumb, a gardening area is a great addition. You can store your pots, tools, seeds, and even set up a small potting bench.
Office: Maybe you need a quiet space to work on your laptop or manage your finances. A small office tucked away in the corner of your pole barn can be a great solution.
Don't forget the doors:
You'll need to think about access. How will you get your stuff in and out of the pole barn? Do you need a big overhead door for large vehicles or equipment? Consider multiple doors, maybe even a pedestrian door for easy access.
Now, let's talk about materials:
Pole barn construction: The classic pole barn uses sturdy posts, usually made from pressure-treated lumber. These posts are driven deep into the ground to support the roof and walls.
Framing and sheathing: Once the posts are in place, you'll need to frame the walls and roof. This involves adding beams and joists to create the structure. The sheathing, usually plywood or OSB board, goes on top of the framing to create a solid base for the exterior and interior finishes.
Roofing: You'll need a durable roofing system that can withstand the elements. Metal roofing is a popular choice for pole barns because it's long-lasting, easy to maintain, and looks great.
Siding: There are tons of options for siding, from simple metal panels to traditional wood siding. Choose a material that complements your home and meets your budget.
Adding the finishing touches:
Insulation: If you plan on using your pole barn year-round or for storage that needs temperature control, you'll want to insulate it. This will make your pole barn more comfortable and efficient.
Interior finishes: You can choose from a variety of interior finishes to give your pole barn a custom look. Drywall, wood paneling, and even painted concrete are all popular options.
Lighting: Good lighting is essential. Consider installing overhead lighting in each room for adequate illumination.
Let's talk about the design:
Ventilation: Proper ventilation is important for keeping the air circulating and preventing moisture buildup.
Windows: Don't underestimate the power of windows! They can brighten up your pole barn and provide natural light.
Flooring: Concrete floors are common in pole barns, but you can also install wood flooring, epoxy coatings, or even rubber mats if you need a more finished look.
Think about safety:
Fire extinguishers: Place fire extinguishers strategically throughout your pole barn.
First aid kit: Keep a well-stocked first aid kit on hand.
Carbon monoxide detector: If you plan to use your pole barn for a workshop, consider installing a carbon monoxide detector.
Don't forget about the extras:
Shelving and storage solutions: Think about the best way to store your belongings. Shelving, cabinets, and even overhead storage systems can help you maximize your space.
Workbenches and workstations: If you're planning on using your pole barn for a workshop, make sure to include a solid workbench and a comfortable workstation.
Electrical outlets: Don't forget to plan for adequate electrical outlets, including dedicated circuits for power tools and other appliances.
Now, you're ready to go!
Designing a pole barn with multiple rooms for storage is a fun project. Take your time, think through your needs, and you'll have a custom space you'll love for years to come.
Bonus Tip:
Don't be afraid to seek out professional help if you need it. A local contractor can help you with the design, planning, and construction of your pole barn, making sure it meets your specific needs and local building codes.
How to Build a Pole Barn with Minimal Site Preparation

Pole barns, also known as post-frame barns, are renowned for their affordability, durability, and ease of construction. Their simplistic design and minimal foundation requirements make them an attractive option for various purposes, including storage, workshops, garages, and even living spaces. This guide aims to equip you with the knowledge necessary to erect a pole barn with minimal site preparation, emphasizing practicality and efficiency.
Understanding Site Preparation for Pole Barns
While pole barns require less extensive site preparation compared to conventional structures, careful consideration must be given to ensure stability and longevity. The primary focus should be on:
1. Ground Condition Assessment:
- Soil Type: Analyze your soil type. Clay soils necessitate thorough compaction and drainage solutions, while sandy soils may require additional support measures.
- Water Table: A high water table can impact foundation stability. It's crucial to understand the groundwater level and address any potential issues through proper drainage techniques.
- Slope: A gently sloping site promotes natural drainage and prevents water accumulation around the structure. Consider grading if your site has a significant slope.
2. Drainage Systems:
- Surface Drainage: Implement adequate surface drainage to divert water away from the foundation and prevent erosion. This might involve grading, installing gutters, downspouts, and swales.
- Subsurface Drainage: In areas with high groundwater levels, a French drain system can effectively channel water away from the building's foundation.
3. Foundation Considerations:
- Concrete Piers: Pole barns typically utilize concrete piers as foundations for the posts. These piers should be properly spaced and extend below the frost line to prevent heaving.
- Frost Depth: The frost line refers to the depth at which the ground freezes in winter. Piers need to be positioned below this depth to avoid frost heave, which can compromise structural integrity.
- Foundation Plan: Ensure the foundation plan aligns with local building codes and regulations. A professional engineer can provide design specifications for your specific location and building requirements.
Minimal Site Preparation Strategies
1. Utilizing Existing Grade:
- Natural Leveling: If your site has a relatively level surface, you can minimize grading work by choosing a suitable building footprint and adjusting the height of the posts to accommodate minor variations in elevation.
- Compaction Techniques: Compacting the ground with a plate compactor or heavy rollers ensures a solid base for the foundation piers.
2. Foundation Options:
- Precast Concrete Piers: Precast piers offer a time-saving and cost-effective option, reducing on-site concrete work.
- Modular Concrete Piers: These prefabricated piers come in various sizes and can be easily installed with minimal site preparation.
3. Optimizing Drainage:
- Simple Drainage Channels: Create shallow drainage channels around the perimeter of your building to direct water away from the foundation.
- Gravel Fill: Utilize gravel fill around the foundation to improve drainage and prevent soil erosion.
Construction Process with Minimal Site Preparation
1. Site Layout: Precisely mark the location of your pole barn using stakes and string lines. Ensure that the layout aligns with your building plan and meets any zoning regulations.
2. Foundation Installation:
- Pier Placement: Excavate holes for the concrete piers according to your foundation plan.
- Concrete Placement: Pour concrete into the prepared holes and ensure proper curing time before proceeding.
3. Post Erection:
- Post Selection: Choose pressure-treated or other durable wood posts that are suitable for your climate and intended use.
- Post Installation: Securely attach the posts to the concrete piers using heavy-duty hardware.
4. Roof Framing:
- Truss System: Utilize prefabricated roof trusses for efficient construction. These trusses are readily available and simplify the roofing process.
- Ridge Beam Installation: Securely attach the ridge beam to the posts, creating the framework for the roof.
- Rafter Installation: Install the roof rafters to the ridge beam and posts.
5. Roofing and Siding:
- Roofing Materials: Select roofing materials that align with your budget and desired aesthetic. Common options include metal roofing, asphalt shingles, and standing seam metal panels.
- Siding Options: Choose from a variety of siding materials, including wood, vinyl, and metal.
6. Finishing Touches:
- Doors and Windows: Install doors and windows that meet your specific needs and complement the building's design.
- Interior Finishes: Complete the interior by adding insulation, drywall, flooring, and any desired fixtures.
Tips for Success with Minimal Site Preparation:
- Professional Consultation: Consult with a qualified builder or architect for professional guidance and advice throughout the process.
- Local Building Codes: Ensure compliance with local building codes and regulations to avoid potential issues and ensure safety.
- Weather Considerations: Be mindful of weather conditions and plan accordingly. Protect the building materials and equipment during inclement weather.
- Detailed Planning: Invest time in meticulous planning and create a comprehensive construction schedule.
Conclusion
Building a pole barn with minimal site preparation is achievable through careful planning, efficient techniques, and understanding the specific requirements of your project. By adhering to the principles outlined in this guide, you can successfully erect a durable, versatile, and cost-effective structure that meets your needs and enhances your property. Remember to prioritize safety, quality, and compliance with building codes throughout the construction process.
How to Build a Pole Barn with a Modular Design for Flexibility
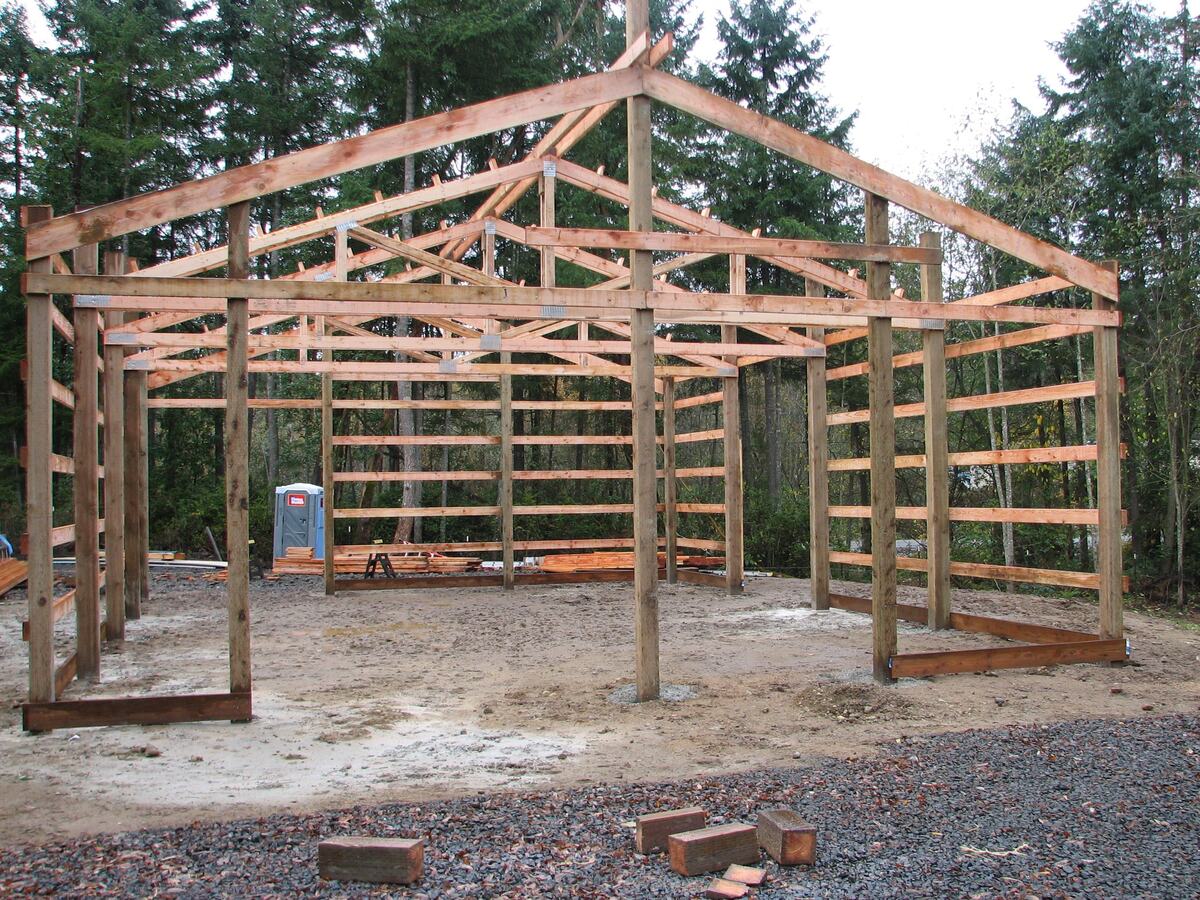
The pole barn, with its simplicity and versatility, has become a mainstay in rural and suburban landscapes alike. Beyond its traditional function as a storage space for farm equipment and vehicles, the modern pole barn offers a myriad of possibilities, from workshops and garages to guest houses and even multi-family dwellings. However, to truly unlock the potential of this adaptable structure, incorporating a modular design becomes paramount. This approach offers a remarkable degree of flexibility, allowing the owner to customize the space to suit evolving needs and preferences.
Understanding the Advantages of Modular Design:
A modular approach to pole barn construction involves building the structure in distinct, self-contained units that can be easily assembled and reconfigured. This approach offers a number of advantages over traditional, monolithic designs:
Flexibility and Adaptability: Modular sections can be rearranged, expanded, or even removed entirely, making the barn readily adaptable to changes in use or storage requirements.
Cost-Effectiveness: The ability to add or modify sections as needed allows for phased construction, spreading out the costs over time. Furthermore, prefabricated modular components can be readily sourced and assembled, potentially reducing labor costs.
Speed of Construction: The modular nature of the design simplifies the building process, leading to faster construction times and earlier occupancy.
Customization: The modular design allows for customization of the interior layout, making it ideal for a variety of purposes.
Essential Considerations for Modular Pole Barn Design:
While the benefits of modular design are undeniable, careful planning and consideration are crucial to ensure success:
Planning and Design: Before starting construction, it is essential to develop a comprehensive plan that outlines the desired layout, size, and features of the barn. Consider the current and potential future uses of the space, ensuring that the modular design accommodates those needs.
Foundation Design: While traditional pole barns often rely on simple concrete piers, modular designs necessitate a sturdier foundation that can accommodate the weight and movement of individual modules. Consider utilizing a continuous concrete foundation or a robust system of interlocking piers.
Modular Unit Design: Each module should be a self-contained unit with its own roof, walls, and structural components. This modularity ensures that sections can be easily added or removed without compromising the structural integrity of the overall barn.
Connecting Modules: Effective connections between modules are crucial for ensuring stability and maintaining the integrity of the structure. Various methods exist, including interlocking frames, steel brackets, and specialized connectors.
Utilities and Services: Consider the placement of utilities and services, such as electricity, plumbing, and HVAC systems, to ensure they are easily accessible and adaptable to future changes.
Modular Pole Barn Design Examples:
Here are a few examples of how modular design can be utilized for different applications:
Workshops and Garages: Modular sections can be used to create specific work areas, storage compartments, or even dedicated spaces for different types of equipment.
Guest Houses and Apartments: Modular units can be joined to create self-contained living spaces, allowing for flexible accommodation and potential future expansion.
Commercial Spaces: Modular designs can be used to create flexible office spaces, retail stores, or even industrial facilities.
Construction Process for a Modular Pole Barn:
Constructing a modular pole barn involves several key steps:
1. Site Preparation: Clear the construction site, excavate for the foundation, and install utilities.
2. Foundation Installation: Install the foundation according to the design plans.
3. Module Construction: Assemble the modular units off-site, ensuring they are properly insulated and finished.
4. Module Transport and Installation: Transport the pre-constructed modules to the site and carefully install them on the foundation.
5. Interconnection: Connect the modules securely, ensuring they are structurally sound.
6. Roofing and Siding: Install the roofing and siding materials, completing the exterior of the barn.
7. Interior Finishing: Add interior walls, insulation, flooring, and other finishing touches as desired.
Choosing Materials for a Modular Pole Barn:
The choice of materials for a modular pole barn is crucial for both structural integrity and aesthetic appeal. Here are some considerations:
Posts and Beams: Choose durable and weather-resistant materials such as pressure-treated lumber, steel, or concrete for the posts and beams.
Roofing: Opt for materials like metal roofing, shingles, or tile, considering factors like durability, maintenance requirements, and aesthetic preference.
Siding: Various siding options exist, ranging from traditional wood siding to modern metal or composite materials.
Insulation: Ensure proper insulation to improve energy efficiency and create a comfortable interior environment.
Conclusion:
Building a pole barn with a modular design offers a unique blend of flexibility, cost-effectiveness, and adaptability. By carefully planning and considering the design elements discussed above, you can create a structure that not only meets your current needs but also allows for seamless future expansion, customization, and adaptation. The modular approach unlocks the full potential of the pole barn, enabling you to create a truly bespoke structure that evolves with your needs and aspirations.