Thursday, November 21, 2024
How to Build a Basic Shed for Your Outdoor Storage Needs

Building Your Dream Shed: A Step-by-Step Guide
Hey there, fellow DIY enthusiasts! So, you're thinking about building a shed? Fantastic! It's a really rewarding project, and the sense of accomplishment when it's finally finished is amazing. Plus, you'll have a fantastic space for all that garden clutter, your tools, or even a little workshop. This guide will walk you through building a basic shed, perfect for beginners. Don't worry, we'll keep it simple and straightforward.Planning and Preparation: The Foundation of Success
Before you even think about picking up a hammer, some serious planning is needed. This isn't just about measuring twice and cutting once (although that's important too!), it's about making sure everything is legally sound and you've got a solid plan to work from.Choosing Your Shed Location
Where will your shed live? This is a crucial decision. Consider:- Accessibility: Do you need easy access from your house or garage?
- Sunlight: Do you want a sunny spot, or would shade be better?
- Ground conditions: Is the ground level and stable? You might need to do some leveling.
- Local regulations: Check with your local council about building permits, setbacks (how far from your property line you can build), and any other restrictions.
Designing Your Shed: Size and Materials
How big do you need your shed to be? This depends entirely on what you plan to store in it. Think about the dimensions carefully. A smaller shed is easier and cheaper to build, but a bigger one will obviously offer more storage space. When choosing materials, pressure-treated lumber is a great option for the frame because it's resistant to rot and insects. For the cladding (the outer covering), you could use anything from more pressure-treated wood to metal or even plastic sheeting â" it really depends on your budget and aesthetic preferences. I recommend sketching out a rough design, noting all the dimensions.Laying the Foundation: A Solid Start
A sturdy foundation is vital for a long-lasting shed. There are a few options:Concrete Slab Foundation
This is the most robust option, but also the most expensive and time-consuming. It involves pouring a concrete slab according to your shed's dimensions. This is a job best left to professionals unless you have experience with concrete work.Gravel Base Foundation
This is a more budget-friendly and simpler alternative. It involves excavating the area, laying down a layer of gravel (compacted thoroughly!), and then adding a layer of paving slabs or concrete pavers on top. This method works well for lighter sheds.Pier and Beam Foundation
This method involves setting concrete piers in the ground at each corner and along the sides of your shed. Wooden beams are then placed on top of the piers to create a framework for your shed floor. This is a good compromise between cost and sturdiness.Building the Frame: The Shed's Skeleton
Once your foundation is set, it's time to construct the frame. This is where accurate measurements and careful cutting become crucial.Cutting and Assembling the Walls
Using your pre-cut lumber, assemble the wall frames, making sure all corners are square and secure. Use appropriate screws and connectors to create strong joints. It might be helpful to build the walls flat on the ground for easier assembly.Erecting the Walls
Carefully lift and position your assembled walls onto the foundation. You might need an extra pair of hands for this part! Ensure they are plumb (perfectly vertical) and use temporary supports to keep them in place until they are secured to the base plates.Building the Roof Frame
The roof frame is typically constructed separately, either as a gable roof (with a triangular shape) or a shed roof (with a single slope). Again, precise measurements are key. Youâll need to cut rafters (for a gable roof) or roof joists (for a shed roof) to the correct angles and lengths.Attaching the Roof to the Walls
Once the roof frame is complete, carefully lift it onto the walls and secure it firmly in place.Cladding and Finishing Touches: Bringing Your Shed to Life
With the frame complete, it's time to add the finishing touches.Adding the Cladding
This is where your chosen cladding material comes into play. Whether youâre using wood, metal, or plastic, follow the manufacturerâs instructions for installation. Pay attention to overlapping the sheets to ensure waterproofing.Adding Doors and Windows
Install your doors and windows, ensuring they are properly sealed to prevent drafts and leaks.Finishing Touches
Consider adding a floor, painting or staining the exterior, adding a lock for security, and installing shelving inside.Commonly Asked Questions
Q: Do I need a building permit? A: This depends on your local regulations. It's always best to check with your local council before starting any construction project.
Q: How long does it take to build a shed? A: The time it takes varies greatly depending on the size and complexity of your shed, as well as your experience. A simple shed could take a weekend, while a more complex one might take several weekends.
Q: What tools do I need? A: Youâll need basic carpentry tools like a hammer, saw, screwdriver, measuring tape, level, and drill. More specialized tools might be necessary depending on your chosen materials and design.
Q: How much does it cost to build a shed? A: The cost varies significantly based on size, materials, and the type of foundation you choose. Expect to spend anywhere from a few hundred to several thousand dollars.
Q: Can I build a shed by myself? A: While itâs possible, itâs often easier and safer to have a helper, especially for lifting heavy materials. If you lack experience, consider seeking help from a more experienced DIYer or even hiring a professional for certain aspects of the project.
Remember, building a shed is a journey, not a race. Take your time, enjoy the process, and you'll end up with a fantastic outdoor storage solution you can be proud of! Happy building!How to Build a Wood Pallet Shed: Simple, Practical, and Budget-Friendly
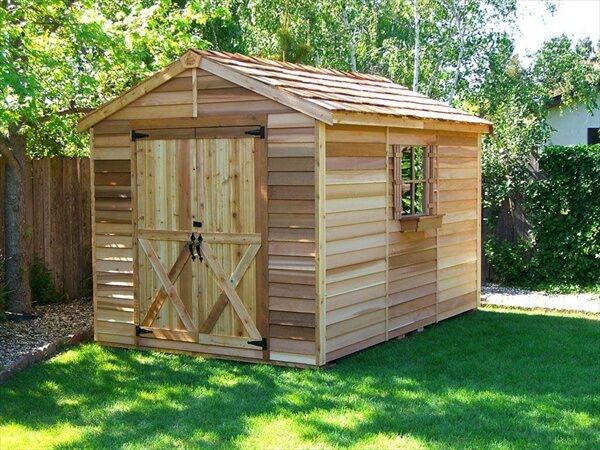
Constructing a Budget-Friendly Wood Pallet Shed: A Comprehensive Guide
The desire for additional storage space is a common theme among homeowners and property owners alike. Traditional shed construction can prove costly and time-consuming. However, a resourceful and practical alternative exists: constructing a shed from reclaimed wood pallets. This guide provides a detailed, step-by-step approach to building a functional and aesthetically pleasing pallet shed, minimizing costs while maximizing practicality.
I. Planning and Preparation: Laying the Foundation for Success
Before commencing construction, meticulous planning is paramount. This phase ensures the project proceeds smoothly and yields a structurally sound and aesthetically pleasing result. Careful consideration must be given to several key aspects:
A. Shed Design and Dimensions
The dimensions of your pallet shed will be dictated primarily by the available space and your storage needs. Sketching a basic design, including the overall dimensions (length, width, and height), door placement, and window placement (if desired), is a crucial first step. Consider the number and size of pallets required to achieve your desired dimensions. Remember to factor in the thickness of the pallet wood when calculating the final dimensions. Standard pallet sizes are readily available, making them convenient for planning.
B. Site Selection and Ground Preparation
Selecting an appropriate site is critical for both structural integrity and ease of access. Choose a level area with good drainage to prevent water accumulation and potential damage to the shed. Clear the area of any debris, vegetation, or obstructions. For a more permanent structure, consider preparing a concrete slab foundation. For a simpler, temporary structure, a compacted gravel base will suffice. The chosen base will significantly impact the longevity and stability of the shed.
C. Material Acquisition and Assessment
The core material for this project is reclaimed wood pallets. Inspect each pallet thoroughly for signs of rot, pest infestation, or significant damage. Select only pallets in good condition, ensuring they are structurally sound for use in construction. You may need to source pallets from multiple locations, and the quality may vary. It's advisable to acquire more pallets than initially anticipated to account for potential damage or unusable sections. Supplemental materials, including nails, screws, wood sealant, and paint (optional) should also be gathered.
II. Construction Phase: Assembling the Pallet Shed
Once the preparatory phase is complete, the construction process can begin. This involves several distinct stages, each requiring careful attention to detail:
A. Base Construction
Constructing a sturdy base is crucial for the structural integrity of the entire shed. If using a concrete slab, ensure it's level and properly cured before proceeding. For a gravel base, compact the gravel thoroughly to provide a stable foundation. The initial layer of pallets will serve as the shed's floor. Secure them to the base using appropriate fasteners, ensuring a level and stable surface. For improved stability and water resistance, consider adding a layer of plywood or pressure-treated lumber on top of the pallet floor.
B. Wall Construction
The pallet walls are constructed by stacking pallets vertically. Ensure the pallets are aligned and properly secured using nails or screws. Use multiple fasteners per pallet to enhance structural rigidity. Consider reinforcing the corners with additional bracing using sturdy lumber. A plumb bob or level can be used to ensure the walls remain vertical and plumb throughout the construction process. For additional stability, consider using metal corner brackets to strengthen the joints.
C. Roof Construction
The roof design can vary depending on preference and available materials. A simple gable roof is relatively easy to construct. Begin by creating the roof trusses using sturdy lumber and connecting them securely to the top of the walls. The pallets can then be used to create the roof decking, laying them horizontally across the trusses and securing them with nails or screws. Ensure proper overlap to prevent water leakage. Consider adding roofing felt or another waterproof membrane before finishing the roof to further enhance protection against the elements.
D. Door and Window Installation (Optional)
The incorporation of a door and windows significantly enhances the shedâs functionality and aesthetics. If constructing a door from pallets, use sturdy pallets and reinforce the frame. Use appropriate hinges and a latch or lock for security. Windows can be created using pallet sections or purchased pre-made windows. Seal all gaps and openings to prevent drafts and moisture ingress.
III. Finishing Touches: Enhancing Durability and Aesthetics
The final phase involves enhancing the shed's durability, weather resistance, and aesthetic appeal.
A. Sealing and Weatherproofing
Applying a wood sealant or protective coating is vital to safeguard the wood pallets from moisture damage, insect infestation, and weathering. This will significantly extend the lifespan of the shed. Select a high-quality sealant designed for outdoor use. Multiple coats may be necessary for optimal protection. Consider a waterproof membrane beneath the roofing material for added protection against leaks.
B. Painting or Staining (Optional)
Painting or staining the shed not only enhances its aesthetic appeal but can also provide additional protection against the elements. Select a weather-resistant paint or stain suitable for exterior use. Consider applying multiple coats for better durability and color consistency. Choose a color that complements the surrounding environment.
C. Interior Finishing (Optional)
Once the exterior is completed, consider adding interior features to enhance functionality. This might include shelves, hooks for hanging tools, or a workbench. These additions will increase the shed's usability and make it more efficient for storage.
IV. Safety Considerations
Throughout the construction process, prioritize safety. Wear appropriate safety gear, including safety glasses, gloves, and sturdy work boots. Use caution when handling tools and materials. Ensure the work area is well-lit and free of obstructions. Always follow the manufacturerâs instructions for any tools or materials used.
Building a wood pallet shed is a rewarding project that combines practicality, affordability, and environmental consciousness. By following this comprehensive guide and prioritizing meticulous planning and attention to detail, you can successfully construct a durable, functional, and visually appealing storage solution for your property.
Wednesday, November 20, 2024
Free Pallet Shed Plans PDF: Build a Functional and Stylish Shed
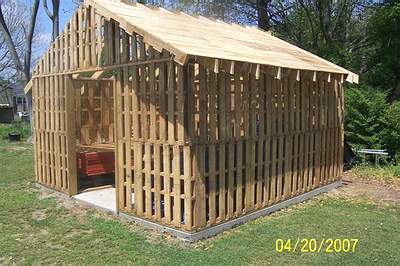
Free Pallet Shed Plans PDF: Build a Functional and Stylish Shed
This comprehensive guide provides detailed instructions and free downloadable PDF plans for constructing a functional and aesthetically pleasing shed utilizing reclaimed pallets. This project offers a cost-effective and environmentally conscious alternative to traditional shed construction, allowing for customization and creative expression.
Assessing Your Needs and Site Preparation
Before embarking on the construction of your pallet shed, careful planning is paramount. This initial phase involves several crucial steps that will directly impact the success and longevity of your project.
Determining Shed Dimensions and Functionality
The dimensions of your shed should be carefully considered based on its intended purpose. Consider the items you plan to store and ensure sufficient space for easy access and maneuverability. Common considerations include the storage of gardening equipment, tools, bicycles, or seasonal items. Sketching a preliminary design, noting the dimensions of your intended storage items, is a highly recommended practice. This will allow you to optimize the internal space and prevent unforeseen spatial constraints.
Site Selection and Ground Preparation
Selecting a suitable location for your shed is critical. Choose a level area with adequate sunlight and drainage. Avoid areas prone to flooding or excessive shade. The ground should be properly leveled and compacted to provide a stable foundation for your shed. Consider the proximity to power sources and water if you plan to incorporate electrical outlets or plumbing. Check local building codes and zoning regulations to ensure compliance with any relevant restrictions.
Material Acquisition and Pallet Assessment
Sourcing your pallets is a crucial step in this cost-effective project. Inspect pallets carefully for structural integrity; damaged or rotten wood is unsuitable. Ensure the pallets are treated for outdoor use. You will likely need a significant number of pallets, so plan your acquisition strategy accordingly. Consider contacting local businesses that frequently receive shipments on pallets, as they may be willing to donate or sell their used pallets at a discounted price.
Constructing the Pallet Shed Frame
The foundation of your pallet shed is its frame. The structural integrity of this frame will directly impact the longevity and stability of your completed shed. This section outlines the critical steps in constructing a robust and durable frame.
Foundation Construction
A solid foundation is essential for a stable shed. You have several options, including a concrete slab, a gravel base, or pressure-treated wooden sleepers. The chosen method will depend on your budget and the ground conditions. A leveled base is crucial, and ensuring proper drainage is imperative to prevent water damage.
Framing the Walls
Using your chosen pallets, begin constructing the walls. Ensure the pallets are securely fastened together using appropriate screws or nails. You may need to disassemble some pallets to achieve the desired dimensions and create openings for doors and windows. Remember to maintain consistent spacing and alignment throughout the construction process for a visually appealing and structurally sound shed.
Erecting the Frame
Once the walls are assembled, carefully erect the frame. This is best achieved with the assistance of another person to ensure stability and prevent accidents. Use temporary bracing to secure the frame until the roof is installed. Ensure the frame is plumb and square using a level and measuring tape. Any imperfections at this stage will significantly impact the final structure.
Roofing and Finishing Touches
The roof and finishing touches significantly enhance both the functionality and aesthetic appeal of your pallet shed. Consider the weather conditions in your area when selecting roofing materials.
Roofing Material Selection and Installation
Several roofing materials are compatible with a pallet shed, including corrugated metal sheeting, asphalt shingles, or even recycled plastic sheeting. Select a material that offers adequate protection from the elements and matches your aesthetic preferences. Ensure proper ventilation to prevent moisture buildup under the roof. Proper installation is crucial to guarantee watertight protection.
Door and Window Installation
Install doors and windows to provide access and natural light. You may use pre-fabricated doors and windows or construct your own from additional pallets and other materials. Ensure that the doors and windows are securely fastened and weatherproofed to prevent drafts and water damage.
Exterior and Interior Finishing
Enhance the durability and aesthetics of your shed through exterior and interior finishing. Consider sealing the wood with a weather-resistant sealant or paint to protect it from moisture and insects. Painting the interior walls can improve the overall appearance and potentially enhance the light reflection within the shed. Add shelving or other organizational features to maximize the storage space.
Safety Precautions and Legal Considerations
Safety is paramount throughout the entire construction process. Adherence to safety guidelines and legal requirements is critical to prevent accidents and ensure compliance.
Safety Gear and Procedures
Always wear appropriate safety gear, including safety glasses, gloves, and sturdy work boots. Use caution when handling power tools and sharp objects. Lift heavy items correctly to prevent back injuries. Follow the manufacturer's instructions for all tools and materials.
Building Permits and Local Regulations
Check with your local authorities regarding building permits and zoning regulations. Some jurisdictions require permits for shed construction, even for smaller structures. Failure to obtain necessary permits may result in fines or legal repercussions. Understand and comply with all local building codes to ensure your shed meets the required safety and structural standards.
Downloading the Free Pallet Shed Plans PDF
The detailed plans for constructing your pallet shed, including diagrams and specifications, are available for free download as a PDF document. [Insert Link to PDF Here]. These plans provide a comprehensive guide to assist you throughout the construction process. Remember to carefully review the plans before starting your project and adapt them to your specific needs and available resources.
Building a pallet shed is a rewarding project that combines functionality, sustainability, and creativity. By following these guidelines and utilizing the provided free PDF plans, you can create a valuable addition to your property that enhances both its aesthetic appeal and practical utility. Remember that careful planning, attention to detail, and adherence to safety standards are essential for a successful project outcome.
Saturday, November 16, 2024
Budget-Friendly 12x20 Shed Plans with Loft for Garden Storage

Budget-Friendly 12x20 Shed Plans with Loft for Garden Storage
This document provides comprehensive plans for constructing a budget-friendly 12x20 shed incorporating a loft for maximized storage capacity. The design prioritizes cost-effectiveness while maintaining structural integrity and functionality, ideal for gardeners needing ample space for tools, equipment, and seasonal items. The detailed plans encompass material lists, construction procedures, and considerations for minimizing expenses throughout the building process.
I. Design Specifications and Considerations
The proposed 12x20 shed design emphasizes practicality and affordability. The dimensions allow for substantial storage space on the ground floor and in the loft area. The inclusion of a loft significantly increases storage capacity without a proportional increase in the footprint of the shed. This design minimizes material waste and simplifies construction. The design can be adapted to suit individual needs and available materials. However, adhering to the specified dimensions and construction techniques will ensure optimal structural integrity and cost-effectiveness.
A. Overall Dimensions and Layout
The shedâs overall dimensions are 12 feet wide by 20 feet long. This allows for ample space for storage on the ground floor and generous headroom in the loft area. The ground floor area will be dedicated to larger equipment and tools, while the loft will be ideal for storing less frequently used items, such as seasonal decorations or excess gardening supplies. The internal layout should allow for easy navigation and efficient access to stored items.
B. Foundation Considerations
A cost-effective foundation solution for this shed is a concrete slab. This provides a solid and level base for the structure, preventing settling and rot. Alternatively, a gravel base with pressure-treated lumber framing can be used as a more economical option, particularly if the ground is well-drained. However, the concrete slab offers superior durability and protection against moisture.
C. Framing and Structure
The shed frame will utilize pressure-treated lumber for durability and resistance to rot and insect infestation. The framing will consist of 4x4 posts for the corners and 2x4 studs for the walls and roof. Standard construction techniques will be employed to ensure structural integrity. The use of readily available lumber sizes minimizes material costs and simplifies construction.
D. Roofing System
A gable roof design is recommended for this shed due to its simplicity and effectiveness in shedding water. This design also allows for the creation of a usable loft space. The roof will be constructed using standard roofing materials such as asphalt shingles or metal roofing. The choice of roofing material will depend on budget and aesthetic preferences, with asphalt shingles generally offering a more economical option.
E. Loft Access and Design
Access to the loft will be via a fixed staircase or a pull-down ladder, depending on budget and space considerations. A fixed staircase offers greater convenience but requires more space and materials. A pull-down ladder is a more cost-effective solution and occupies less floor space. The loft floor will be constructed using plywood or OSB sheathing, providing a sturdy and level surface for storage.
II. Materials List and Cost Estimation
The following is an estimated materials list. Prices will vary depending on location and supplier. It is crucial to obtain accurate pricing from local suppliers before commencing construction. This list serves as a guide and may need adjustments based on individual preferences and local availability.
A. Lumber
- Pressure-treated 4x4 posts: 8
- Pressure-treated 2x4 studs: Approximately 150 linear feet
- Plywood or OSB sheathing for walls and roof: Quantities will vary depending on wall and roof dimensions.
- Plywood or OSB for loft floor: Calculated based on loft dimensions.
- Trim boards: For finishing and aesthetic details
B. Roofing Materials
- Asphalt shingles or metal roofing: Quantity will depend on roof dimensions.
- Roofing felt or underlayment
- Roofing nails or screws
C. Foundation Materials
- Concrete (if using a concrete slab) or gravel (if using a gravel base)
- Rebar (if using a concrete slab)
- Pressure-treated lumber for framing (if using a gravel base)
D. Other Materials
- Exterior siding (e.g., vinyl, wood, metal): Chosen based on budget and aesthetic preferences
- Windows and doors: Size and quantity will depend on design preferences
- Fasteners (nails, screws, bolts)
- Exterior paint or stain
- Ladder or staircase materials (depending on loft access chosen)
Note: This is a partial list. A more detailed and precise materials list should be generated based on finalized design plans and specific supplier quotes.
III. Construction Process
The construction process will follow standard shed-building procedures. Attention to detail and adherence to building codes are essential. Detailed step-by-step instructions are beyond the scope of this document but are readily available from numerous online resources and books. Seeking assistance from experienced builders is recommended, especially for those lacking construction experience.
A. Foundation Preparation
This involves leveling the ground and preparing the chosen foundation (concrete slab or gravel base). The foundation should be sufficiently strong and level to support the shedâs weight.
B. Frame Construction
This involves assembling the walls and roof frame using pressure-treated lumber. Proper framing techniques are crucial for structural stability. Squareness and plumbness should be carefully checked throughout the construction process.
C. Sheathing and Roofing
This involves installing the plywood or OSB sheathing on the walls and roof, followed by the chosen roofing material. Proper installation techniques are crucial for weatherproofing and structural integrity.
D. Loft Construction
This involves building the loft floor using plywood or OSB sheathing, supported by appropriate framing. Ensure sufficient headroom and safe access to the loft area.
E. Siding and Finishing
This involves installing the chosen exterior siding, windows, and doors, followed by finishing touches such as painting or staining. Proper sealing and weatherproofing are crucial for long-term durability.
IV. Cost-Saving Strategies
Several strategies can be employed to minimize construction costs:
- Source materials from economical suppliers: Compare prices from various lumber yards and home improvement stores.
- Utilize reclaimed or salvaged materials where possible: This can significantly reduce material costs.
- Perform as much of the labor yourself as possible: This eliminates labor costs, although it requires time and skills.
- Prioritize simple designs: Avoid complex designs that require specialized materials or techniques.
- Consider DIY alternatives for some features: For instance, building your own staircase or using a simpler roofing system.
- Plan ahead and purchase materials in bulk: This can often result in significant savings.
By carefully planning and executing the construction process, a functional and aesthetically pleasing 12x20 shed with a loft can be built at a significantly reduced cost. Remember to always prioritize safety and adhere to local building codes.
Monday, November 11, 2024
How to Design a Pole Barn with Multiple Rooms for Storage

Alright, so you're thinking about building a pole barn. Great choice! They're super versatile, and with a little planning, you can turn it into a multi-room storage powerhouse.
Let's start with the basics:
First things first, let's talk about the size. How much stuff do you need to store? Do you need space for a workshop, a gardening area, or maybe a play area for the kids? Once you have an idea of the square footage you need, you can start to think about the layout.
Think like a puzzle:
Imagine your pole barn as a big blank canvas. You'll need to divide this space into different rooms, each with its own purpose. Do you want separate areas for tools, equipment, garden supplies, or maybe even a small office space?
Here's a typical layout to consider:
Main Storage Area: This is your core space. Think of it as the main living room of your pole barn. It's where you'll store the bulk of your stuff, like lawnmowers, bikes, and other seasonal items.
Workshop: If you're handy, a dedicated workshop is a must. You can set up your workbench, tools, and have plenty of room to work on projects.
Gardening Area: If you have a green thumb, a gardening area is a great addition. You can store your pots, tools, seeds, and even set up a small potting bench.
Office: Maybe you need a quiet space to work on your laptop or manage your finances. A small office tucked away in the corner of your pole barn can be a great solution.
Don't forget the doors:
You'll need to think about access. How will you get your stuff in and out of the pole barn? Do you need a big overhead door for large vehicles or equipment? Consider multiple doors, maybe even a pedestrian door for easy access.
Now, let's talk about materials:
Pole barn construction: The classic pole barn uses sturdy posts, usually made from pressure-treated lumber. These posts are driven deep into the ground to support the roof and walls.
Framing and sheathing: Once the posts are in place, you'll need to frame the walls and roof. This involves adding beams and joists to create the structure. The sheathing, usually plywood or OSB board, goes on top of the framing to create a solid base for the exterior and interior finishes.
Roofing: You'll need a durable roofing system that can withstand the elements. Metal roofing is a popular choice for pole barns because it's long-lasting, easy to maintain, and looks great.
Siding: There are tons of options for siding, from simple metal panels to traditional wood siding. Choose a material that complements your home and meets your budget.
Adding the finishing touches:
Insulation: If you plan on using your pole barn year-round or for storage that needs temperature control, you'll want to insulate it. This will make your pole barn more comfortable and efficient.
Interior finishes: You can choose from a variety of interior finishes to give your pole barn a custom look. Drywall, wood paneling, and even painted concrete are all popular options.
Lighting: Good lighting is essential. Consider installing overhead lighting in each room for adequate illumination.
Let's talk about the design:
Ventilation: Proper ventilation is important for keeping the air circulating and preventing moisture buildup.
Windows: Don't underestimate the power of windows! They can brighten up your pole barn and provide natural light.
Flooring: Concrete floors are common in pole barns, but you can also install wood flooring, epoxy coatings, or even rubber mats if you need a more finished look.
Think about safety:
Fire extinguishers: Place fire extinguishers strategically throughout your pole barn.
First aid kit: Keep a well-stocked first aid kit on hand.
Carbon monoxide detector: If you plan to use your pole barn for a workshop, consider installing a carbon monoxide detector.
Don't forget about the extras:
Shelving and storage solutions: Think about the best way to store your belongings. Shelving, cabinets, and even overhead storage systems can help you maximize your space.
Workbenches and workstations: If you're planning on using your pole barn for a workshop, make sure to include a solid workbench and a comfortable workstation.
Electrical outlets: Don't forget to plan for adequate electrical outlets, including dedicated circuits for power tools and other appliances.
Now, you're ready to go!
Designing a pole barn with multiple rooms for storage is a fun project. Take your time, think through your needs, and you'll have a custom space you'll love for years to come.
Bonus Tip:
Don't be afraid to seek out professional help if you need it. A local contractor can help you with the design, planning, and construction of your pole barn, making sure it meets your specific needs and local building codes.
How to Build a Pole Barn with Minimal Site Preparation

Pole barns, also known as post-frame barns, are renowned for their affordability, durability, and ease of construction. Their simplistic design and minimal foundation requirements make them an attractive option for various purposes, including storage, workshops, garages, and even living spaces. This guide aims to equip you with the knowledge necessary to erect a pole barn with minimal site preparation, emphasizing practicality and efficiency.
Understanding Site Preparation for Pole Barns
While pole barns require less extensive site preparation compared to conventional structures, careful consideration must be given to ensure stability and longevity. The primary focus should be on:
1. Ground Condition Assessment:
- Soil Type: Analyze your soil type. Clay soils necessitate thorough compaction and drainage solutions, while sandy soils may require additional support measures.
- Water Table: A high water table can impact foundation stability. It's crucial to understand the groundwater level and address any potential issues through proper drainage techniques.
- Slope: A gently sloping site promotes natural drainage and prevents water accumulation around the structure. Consider grading if your site has a significant slope.
2. Drainage Systems:
- Surface Drainage: Implement adequate surface drainage to divert water away from the foundation and prevent erosion. This might involve grading, installing gutters, downspouts, and swales.
- Subsurface Drainage: In areas with high groundwater levels, a French drain system can effectively channel water away from the building's foundation.
3. Foundation Considerations:
- Concrete Piers: Pole barns typically utilize concrete piers as foundations for the posts. These piers should be properly spaced and extend below the frost line to prevent heaving.
- Frost Depth: The frost line refers to the depth at which the ground freezes in winter. Piers need to be positioned below this depth to avoid frost heave, which can compromise structural integrity.
- Foundation Plan: Ensure the foundation plan aligns with local building codes and regulations. A professional engineer can provide design specifications for your specific location and building requirements.
Minimal Site Preparation Strategies
1. Utilizing Existing Grade:
- Natural Leveling: If your site has a relatively level surface, you can minimize grading work by choosing a suitable building footprint and adjusting the height of the posts to accommodate minor variations in elevation.
- Compaction Techniques: Compacting the ground with a plate compactor or heavy rollers ensures a solid base for the foundation piers.
2. Foundation Options:
- Precast Concrete Piers: Precast piers offer a time-saving and cost-effective option, reducing on-site concrete work.
- Modular Concrete Piers: These prefabricated piers come in various sizes and can be easily installed with minimal site preparation.
3. Optimizing Drainage:
- Simple Drainage Channels: Create shallow drainage channels around the perimeter of your building to direct water away from the foundation.
- Gravel Fill: Utilize gravel fill around the foundation to improve drainage and prevent soil erosion.
Construction Process with Minimal Site Preparation
1. Site Layout: Precisely mark the location of your pole barn using stakes and string lines. Ensure that the layout aligns with your building plan and meets any zoning regulations.
2. Foundation Installation:
- Pier Placement: Excavate holes for the concrete piers according to your foundation plan.
- Concrete Placement: Pour concrete into the prepared holes and ensure proper curing time before proceeding.
3. Post Erection:
- Post Selection: Choose pressure-treated or other durable wood posts that are suitable for your climate and intended use.
- Post Installation: Securely attach the posts to the concrete piers using heavy-duty hardware.
4. Roof Framing:
- Truss System: Utilize prefabricated roof trusses for efficient construction. These trusses are readily available and simplify the roofing process.
- Ridge Beam Installation: Securely attach the ridge beam to the posts, creating the framework for the roof.
- Rafter Installation: Install the roof rafters to the ridge beam and posts.
5. Roofing and Siding:
- Roofing Materials: Select roofing materials that align with your budget and desired aesthetic. Common options include metal roofing, asphalt shingles, and standing seam metal panels.
- Siding Options: Choose from a variety of siding materials, including wood, vinyl, and metal.
6. Finishing Touches:
- Doors and Windows: Install doors and windows that meet your specific needs and complement the building's design.
- Interior Finishes: Complete the interior by adding insulation, drywall, flooring, and any desired fixtures.
Tips for Success with Minimal Site Preparation:
- Professional Consultation: Consult with a qualified builder or architect for professional guidance and advice throughout the process.
- Local Building Codes: Ensure compliance with local building codes and regulations to avoid potential issues and ensure safety.
- Weather Considerations: Be mindful of weather conditions and plan accordingly. Protect the building materials and equipment during inclement weather.
- Detailed Planning: Invest time in meticulous planning and create a comprehensive construction schedule.
Conclusion
Building a pole barn with minimal site preparation is achievable through careful planning, efficient techniques, and understanding the specific requirements of your project. By adhering to the principles outlined in this guide, you can successfully erect a durable, versatile, and cost-effective structure that meets your needs and enhances your property. Remember to prioritize safety, quality, and compliance with building codes throughout the construction process.
How to Build a Pole Barn with a Modular Design for Flexibility
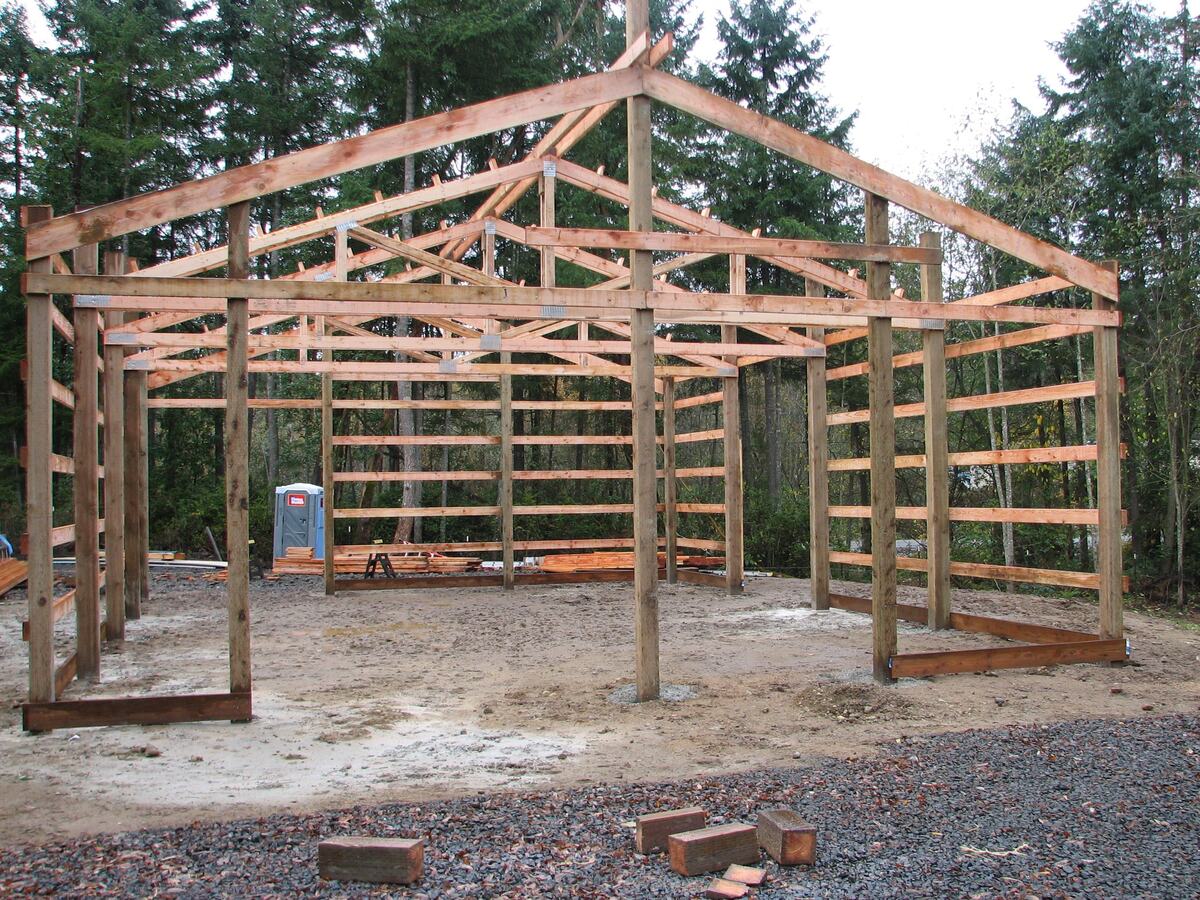
The pole barn, with its simplicity and versatility, has become a mainstay in rural and suburban landscapes alike. Beyond its traditional function as a storage space for farm equipment and vehicles, the modern pole barn offers a myriad of possibilities, from workshops and garages to guest houses and even multi-family dwellings. However, to truly unlock the potential of this adaptable structure, incorporating a modular design becomes paramount. This approach offers a remarkable degree of flexibility, allowing the owner to customize the space to suit evolving needs and preferences.
Understanding the Advantages of Modular Design:
A modular approach to pole barn construction involves building the structure in distinct, self-contained units that can be easily assembled and reconfigured. This approach offers a number of advantages over traditional, monolithic designs:
Flexibility and Adaptability: Modular sections can be rearranged, expanded, or even removed entirely, making the barn readily adaptable to changes in use or storage requirements.
Cost-Effectiveness: The ability to add or modify sections as needed allows for phased construction, spreading out the costs over time. Furthermore, prefabricated modular components can be readily sourced and assembled, potentially reducing labor costs.
Speed of Construction: The modular nature of the design simplifies the building process, leading to faster construction times and earlier occupancy.
Customization: The modular design allows for customization of the interior layout, making it ideal for a variety of purposes.
Essential Considerations for Modular Pole Barn Design:
While the benefits of modular design are undeniable, careful planning and consideration are crucial to ensure success:
Planning and Design: Before starting construction, it is essential to develop a comprehensive plan that outlines the desired layout, size, and features of the barn. Consider the current and potential future uses of the space, ensuring that the modular design accommodates those needs.
Foundation Design: While traditional pole barns often rely on simple concrete piers, modular designs necessitate a sturdier foundation that can accommodate the weight and movement of individual modules. Consider utilizing a continuous concrete foundation or a robust system of interlocking piers.
Modular Unit Design: Each module should be a self-contained unit with its own roof, walls, and structural components. This modularity ensures that sections can be easily added or removed without compromising the structural integrity of the overall barn.
Connecting Modules: Effective connections between modules are crucial for ensuring stability and maintaining the integrity of the structure. Various methods exist, including interlocking frames, steel brackets, and specialized connectors.
Utilities and Services: Consider the placement of utilities and services, such as electricity, plumbing, and HVAC systems, to ensure they are easily accessible and adaptable to future changes.
Modular Pole Barn Design Examples:
Here are a few examples of how modular design can be utilized for different applications:
Workshops and Garages: Modular sections can be used to create specific work areas, storage compartments, or even dedicated spaces for different types of equipment.
Guest Houses and Apartments: Modular units can be joined to create self-contained living spaces, allowing for flexible accommodation and potential future expansion.
Commercial Spaces: Modular designs can be used to create flexible office spaces, retail stores, or even industrial facilities.
Construction Process for a Modular Pole Barn:
Constructing a modular pole barn involves several key steps:
1. Site Preparation: Clear the construction site, excavate for the foundation, and install utilities.
2. Foundation Installation: Install the foundation according to the design plans.
3. Module Construction: Assemble the modular units off-site, ensuring they are properly insulated and finished.
4. Module Transport and Installation: Transport the pre-constructed modules to the site and carefully install them on the foundation.
5. Interconnection: Connect the modules securely, ensuring they are structurally sound.
6. Roofing and Siding: Install the roofing and siding materials, completing the exterior of the barn.
7. Interior Finishing: Add interior walls, insulation, flooring, and other finishing touches as desired.
Choosing Materials for a Modular Pole Barn:
The choice of materials for a modular pole barn is crucial for both structural integrity and aesthetic appeal. Here are some considerations:
Posts and Beams: Choose durable and weather-resistant materials such as pressure-treated lumber, steel, or concrete for the posts and beams.
Roofing: Opt for materials like metal roofing, shingles, or tile, considering factors like durability, maintenance requirements, and aesthetic preference.
Siding: Various siding options exist, ranging from traditional wood siding to modern metal or composite materials.
Insulation: Ensure proper insulation to improve energy efficiency and create a comfortable interior environment.
Conclusion:
Building a pole barn with a modular design offers a unique blend of flexibility, cost-effectiveness, and adaptability. By carefully planning and considering the design elements discussed above, you can create a structure that not only meets your current needs but also allows for seamless future expansion, customization, and adaptation. The modular approach unlocks the full potential of the pole barn, enabling you to create a truly bespoke structure that evolves with your needs and aspirations.
Budget 8x10 shed plans that are simple and affordable
Hey there, fellow DIY enthusiast! Are you looking to add some extra storage space to your backyard without breaking the bank? Well, you've come to the right place! Building your own 8x10 shed is a fantastic way to get the storage you need while also learning some valuable skills and having some fun along the way.
Now, I know what you're thinking: "Building a shed sounds complicated and expensive!" But trust me, it doesn't have to be! With a little planning and some creative thinking, you can build a solid and functional shed that fits your budget.
Let's get started with the basics:
Materials: The key to keeping your shed budget-friendly is to choose the right materials. Pressure-treated lumber for the foundation and floor joists is a must for durability and rot resistance. For the walls and roof, you can opt for regular lumber like pine or spruce. Don't be afraid to check out your local lumberyard for deals and salvaged materials!
Tools: You'll need a basic set of tools for this project, like a saw, drill, hammer, tape measure, level, and some basic hand tools. If you're handy with power tools, even better!
Time: Factor in a few weekends to complete the project. It's not a one-day job, but with a little dedication, you'll be able to get it done.
Now, let's dive into the nitty-gritty of the plans:
1. The Foundation:
Choose your foundation: You have a couple of options here: a concrete slab or a simple pressure-treated wood foundation. Concrete is more expensive but provides a solid and long-lasting base. For a budget-friendly approach, a wooden foundation is a great option.
Prepare the site: Clear the area, level it out, and mark the dimensions for your shed.
Laying the foundation: If you're going with a wood foundation, you'll need to lay down pressure-treated beams as your foundation. Make sure to secure them properly to the ground.
2. The Floor:
Framing the floor: Use pressure-treated 2x8s or 2x10s for the floor joists. Space them 16 inches apart for support.
Sheathing the floor: You can use plywood or OSB (oriented strand board) for the floor sheathing. Make sure the sheets are properly secured to the joists.
3. Walls and Roof:
Framing the walls: You'll need to frame the walls using 2x4s or 2x6s. Cut the studs to the correct height and attach them to the floor joists.
Sheathing the walls: Use plywood or OSB for sheathing the walls. Make sure to add bracing to the walls for stability.
Building the roof: Frame the roof using rafters. You'll need to determine the angle of the roof and ensure the rafters are properly secured.
Sheathing the roof: Use plywood or OSB for sheathing the roof. Make sure the sheets are properly secured to the rafters.
Roofing: For a budget-friendly option, you can use shingles or metal roofing. Make sure to install them according to the manufacturer's instructions.
4. Doors and Windows:
Choosing your doors: You can use a standard pre-hung door for your shed or build your own using lumber and hardware.
Adding windows: You can also install windows for some natural light. Make sure to select windows that are weatherproof.
5. Finishing Touches:
Siding: You can choose from a variety of siding materials for your shed, including vinyl, wood, or metal.
Painting: Add some color and personality to your shed with a fresh coat of paint.
Adding trim: Trim will give your shed a finished look and help protect the edges from weather damage.
Tips for Keeping Your Shed Budget-Friendly:
Shop around for materials: Compare prices at different lumberyards and home improvement stores.
Consider using salvaged materials: Look for used building materials at salvage yards or online marketplaces.
Do the work yourself: You'll save money on labor costs by doing the work yourself.
Get creative with design: Don't be afraid to think outside the box and use your own creativity to build a unique and budget-friendly shed.
Remember, this is just a basic outline of the shed building process. You can always adjust the plans and materials to fit your budget and your preferences.
There are many resources available online and in libraries that can provide you with more detailed plans and instructions.
Building your own shed is a rewarding experience. It's a chance to learn new skills, save money, and create a valuable addition to your property.
So what are you waiting for? Get started on your DIY shed project today!
Sunday, November 10, 2024
Diy 10x12 shed plans for creating extra storage

Hey there, fellow storage-challenged folks! You know the feeling, right? Clutter creeping in, boxes piling up, and your garage looking like a bomb went off in a toy factory. Well, I'm here to tell you - building your own 10x12 shed is the answer! It's not as intimidating as you might think, and the satisfaction of crafting your own storage solution is truly rewarding.
Let's dive in and break down this DIY adventure step by step.
### Planning Your Dream Shed:
First things first, let's get those creative juices flowing!
Location, Location, Location: Where will your shed live? Consider sunlight, drainage, proximity to your house, and any pesky trees that might get in the way.
Foundation Fun: We're going with a simple, budget-friendly foundation. A concrete slab is perfect for a 10x12 shed, offering stability and a solid base.
Roofing Rhapsody: A simple gable roof is easy to build and offers great water drainage. You can even add a dormer window for extra headroom and natural light.
Shed Style: Think about the overall look. Do you want a classic, traditional shed or something a little more modern? Pinterest is your friend for inspiration!
The Essentials: You'll need your basic tools: hammer, drill, saw, tape measure, level, etc. A good set of safety glasses and gloves are must-haves.
### Step-by-Step Construction:
Okay, now let's build!
1. Foundation Frenzy:
Marking the Ground: Use stakes and string to mark the perimeter of your shed on the ground. Double-check everything to ensure your shed is square.
Pouring the Slab: Now, it's time to pour the concrete slab. This might require some heavy lifting, so enlist a friend for help. Make sure the slab is level and slightly sloped for drainage.
2. Framing Frenzy:
Building the Walls: Start by cutting your wall studs to the correct length. Use a stud finder to locate existing walls or utilities, making sure your shed doesn't interfere with anything.
Constructing the Floor: Lay down a layer of plywood for the floor and secure it to the joists. Make sure your floor is level before moving on.
Raising the Walls: With a helper, carefully raise the walls and brace them with temporary supports.
Sheathing It Up: Apply plywood sheathing to the exterior walls for extra strength and stability.
3. Roofing Revelations:
Rafter Time: Cut and install the rafters, making sure they're spaced correctly for support.
Sheathing the Roof: Apply plywood sheathing to the roof, ensuring it's securely attached.
Adding the Roof Deck: Now for the final roof layer! Consider a durable option like shingles or metal roofing. Don't forget the flashing around the chimney, if you have one!
4. Finishing Touches:
Adding the Doors: You'll be able to access your shed through its double doors!
Windows: Install windows for light and ventilation.
Siding: Choose your siding style and color, and apply it to the exterior walls.
The Interior: Paint the interior walls to match your aesthetic, and consider adding shelves or hooks for organization.
5. Time to Celebrate!:
You did it! You've built your very own 10x12 shed. Now it's time to celebrate your hard work and admire your new storage space.
Extra Tips:
Ventilation is Key: Remember to install vents in the roof and walls for proper air circulation.
Electricity: You can add electrical outlets to your shed for lighting or power tools, but remember to hire a qualified electrician.
Insulation: Consider adding insulation to the walls and roof for added warmth in colder months.
Safety First: Always wear safety gear, double-check your measurements, and don't be afraid to ask for help when needed.
### Enjoy Your New Storage Haven!
Building a 10x12 shed is a rewarding and practical project. Not only will you have a fantastic new storage space, but you'll also gain valuable DIY skills and a sense of accomplishment. So go ahead, grab your tools, and start building your dream storage haven!
Remember: This guide is a starting point. Always consult with local building codes and regulations before starting your project. And if you're not comfortable with certain aspects of the construction, don't hesitate to hire professionals for those specific tasks.
Happy building!
Saturday, November 9, 2024
10x12 shed plans: how to build your own for less
Hey there, DIY enthusiasts! So, you're thinking about building a 10x12 shed, eh? You're in the right place! Building your own shed is an awesome way to get a super useful space without breaking the bank. Plus, there's something really satisfying about seeing your hard work come to life, brick by brick (or should I say, board by board?).
Let's dive in and break down this project into manageable steps. I'm not going to overwhelm you with super technical jargon â" think of this as a friendly guide, like having a buddy alongside you on this journey.
1. Laying the Foundation:
The foundation is like the bedrock of your shed. You want it to be strong and level to avoid any wobbly walls. There are a few options here:
Concrete Slab: This is the most robust option and perfect if you're planning on a heavy-duty shed. It's a bit more work and needs some know-how, but trust me, it's worth it for long-term stability.
Concrete Pier Foundation: This is a great middle ground. You'll create individual concrete piers at strategic locations and then rest your floor joists on top. It's easier to work with than a slab and still offers good support.
Pressure-Treated Wood Piers: This is the simplest and most budget-friendly option. You'll use pressure-treated wood to create the piers and then rest your floor joists on top. Just make sure you're using the right grade of lumber for durability.
2. Framing Up Your Walls:
Now, it's time to start building your walls. Get your lumber ready (we're talking 2x4s and 2x6s, usually!), and don't forget your stud finder!
Cutting and Assembling Walls: You'll need to cut your lumber to the right lengths for your walls. Then, you'll assemble them using nails or screws, creating sturdy frames. It's a good idea to double-check your measurements and make sure everything's square and level.
Sheathing the Walls: This is like giving your walls a protective layer. You'll attach plywood or OSB sheathing to the wall frames, giving them additional strength and creating a surface for your siding to attach to.
3. The Floor: A Solid Base
Time to build that floor! It's a pretty straightforward process, but don't skip any steps.
Laying the Floor Joists: These are the beams that will run across your shed, providing support for your floorboards. They're usually spaced 16 inches apart.
Subfloor: You'll lay down plywood or OSB boards on top of the joists, creating a sturdy subfloor that's ready for your finished floor.
Finishing Touches: If you're planning on having a finished floor, now's the time to add it! You can go with wood flooring, concrete, or even tiles â" the choice is yours!
4. The Roof: Keeping Things Dry
A good roof is essential for keeping your shed protected from the elements. This is where things can get a bit more involved, but don't worry, it's still manageable.
Rafters and Truss System: This is the backbone of your roof. You'll be creating a system of rafters or trusses that will support your roof sheathing and shingles.
Roof Sheathing: This is the layer that goes on top of the rafters or trusses and provides a solid base for your roofing material.
Shingles or Roofing Material: There are lots of options here â" asphalt shingles, metal roofing, or even wood shakes. Choose what fits your style and budget!
5. Siding and Trim: Finishing Touches
We're nearing the end! Now, it's time to give your shed that final, polished look.
Siding: This is the visible outer layer of your shed. You can go with vinyl siding, wood siding, or even a more rustic look with rough-sawn lumber.
Trim: This is the finishing touch that adds a touch of style to your shed. You can use trim around the doors, windows, and edges to create a clean and polished look.
6. Doors and Windows: Let the Light In
Now, let's add those doors and windows for easy access and natural light!
Door Installation: This is a two-person job. You'll need to measure carefully and install the door frame and the door itself.
Window Installation: Just like doors, windows need precise measurements for a seamless installation.
7. Finishing Up:
You're almost there! Now, let's wrap up the final details.
Painting or Staining: This is where you can truly personalize your shed! Choose your favorite color or stain to add a touch of character.
Interior Finishing: Decide how you want to finish the inside of your shed. You might want to add insulation for warmth and soundproofing, or maybe you'll just leave it as a clean, open space.
Tips and Tricks:
Plan and Measure: Before you even start, take your time to plan and measure everything carefully. It's much easier to make changes on paper than on a half-built shed!
Don't Rush: Building a shed takes time. Don't try to rush the process; enjoy it!
Safety First: Always prioritize safety. Wear safety glasses, gloves, and sturdy shoes.
Ask for Help: Don't be afraid to ask for help if you need it. Having an extra pair of hands can make a big difference, especially with heavier tasks.
Celebrate Your Success: Once you're done, take a moment to admire your hard work! You've just built your very own 10x12 shed!
Cost Considerations:
Building your own shed is a great way to save money, but it's important to budget realistically. The cost of materials can vary depending on where you live and the quality of the materials you choose. Here's a breakdown of approximate costs (keep in mind, these are rough estimates):
Lumber: $500-1000
Foundation materials (concrete, piers, etc.): $200-500
Roof sheathing and shingles: $200-400
Siding: $200-400
Doors and windows: $200-500
Hardware (screws, nails, etc.): $100-200
Overall, you could build a 10x12 shed for around $1500-3000, depending on your choices.
Remember: Building a shed is a journey, not a race. Take your time, enjoy the process, and don't be afraid to ask for help. You'll be amazed at what you can accomplish with a little planning, hard work, and a positive attitude. Now go forth and build!
Friday, November 8, 2024
The best affordable 8x12 shed plans that actually work
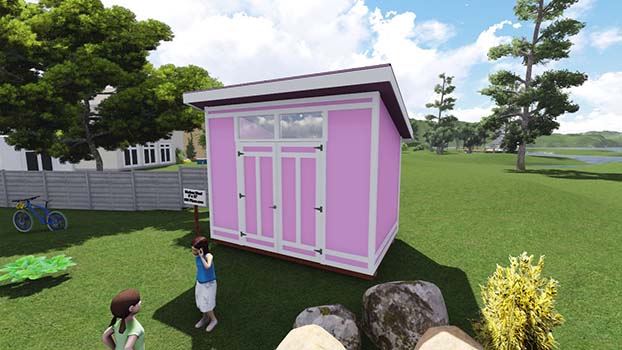
Alright, so you're ready to tackle that shed project, huh? You've got the vision, the determination, and maybe even a little bit of intimidation. Don't worry, we've got your back! Building a shed is a super rewarding project, especially when you can do it yourself and save a bunch of cash.
And who doesn't love a good 8x12 shed? It's the Goldilocks of shed sizes: big enough for all your stuff, but not so big it becomes a massive undertaking.
But let's be real, finding affordable plans that actually work can be a pain. You've got to wade through websites with confusing jargon and half-baked instructions. Plus, you want to be sure those plans actually come with everything you need to succeed.
That's why I'm here to spill the tea on finding the best affordable 8x12 shed plans that actually work. We're talking about plans that are clear, concise, and won't leave you scratching your head halfway through construction.
What to Look for in a Plan
Here's the deal: a good plan is your roadmap to success. Think of it like a recipe, but instead of a delicious meal, you're crafting a storage masterpiece. Here are some key ingredients for the perfect shed plan:
Detailed Drawings: Forget blurry sketches! You need clear, well-labeled drawings of every angle, wall, and detail of your shed. These should show you exactly how the pieces fit together.
Material List: This is your shopping list. It should include all the necessary materials (wood, fasteners, shingles, etc.) with their exact dimensions and quantities. No more guessing or extra trips to the lumberyard!
Step-by-Step Instructions: A well-written plan will guide you through every step, from foundation to finishing touches. The instructions should be easy to follow and include helpful diagrams and photos.
Foundation Options: Choose a plan that provides different foundation options so you can pick the one that suits your budget and soil conditions. You can go with a simple concrete slab, treated lumber skids, or even a block foundation.
Building Code Compliance: Make sure the plans comply with your local building codes. This ensures your shed is safe and legal.
Finding the Right Plan
Now, where do you find these magical plans? Here are some excellent options:
DIY Shed Plans Websites: There are tons of online resources dedicated to shed plans. Some offer free plans, while others charge a small fee.
Lumber Yards: Many lumberyards offer free or low-cost plans for their customers. They might even have a selection tailored to the materials they stock.
Home Improvement Stores: Big box stores often have free plans available online or in their stores. They may also offer construction workshops to help you get started.
Shed Building Books: These are great for a comprehensive approach. You'll find detailed explanations, construction techniques, and inspiration for your shed design.
Important Tips for Success
Alright, you've found your perfect plan. Here's how to make sure your journey is smooth sailing:
Read Everything: Go through the plans thoroughly before you even start buying materials. This ensures you understand every step and have all the necessary information.
Gather Your Tools: Make a list of the tools you'll need based on the plan's instructions. You might need a saw, drill, hammer, level, tape measure, and other essential tools.
Safety First: Always wear safety glasses, gloves, and appropriate work gear. Remember to follow safe lifting practices and use proper construction techniques.
Take Your Time: Building a shed is a marathon, not a sprint. Don't rush the process. Take breaks when needed, and enjoy the journey.
Building Your 8x12 Dream Shed
With the right plan and a little elbow grease, you can create a truly amazing shed. Here are some tips for maximizing your 8x12 space:
Storage Solutions: Use shelves, drawers, and bins to keep your belongings organized. You can even build a workbench or pegboard for additional functionality.
Natural Light: Consider adding windows for natural light. They also add a touch of elegance and make the space feel bigger.
Ventilation: Proper ventilation is key for avoiding moisture buildup and keeping the shed cool. Install a vent in the roof or wall for optimal air circulation.
Electrical Outlets: Add electrical outlets for power tools, lights, or even a small heater.
The Final Touches
Once the walls are up, the roof is on, and the finishing touches are in place, you'll have a masterpiece. Don't be afraid to add personal touches:
Paint: Choose a paint color that complements your home or reflects your style.
Landscaping: Add some landscaping around your shed to make it blend in with your yard. You could plant flowers, shrubs, or a small garden.
Decor: Personalize the interior with some decorative touches. Hang up pictures, add a rug, or even install a small hanging light fixture.
The Joy of Building Your Own Shed
You've done it! You built your very own 8x12 shed. It's a space to escape, organize, create, or simply relax. It's a testament to your skills, dedication, and a whole lot of pride.
So, grab those plans, gather your tools, and start building your dream shed! You'll be surprised at what you can accomplish with a little bit of planning and effort. And when you're done, you'll be ready to celebrate with a well-deserved cup of coffee or a cold beer.
Thursday, November 7, 2024
How to design a custom 10x12 garden shed yourself

Okay, so you've got the itch. You want a garden shed, not just any old shed, but YOUR shed. A custom 10x12 masterpiece, a haven for your tools, your plants, maybe even your weekend craft projects. You're picturing it already, aren't you? The smell of fresh wood, the satisfying thunk of the hammer, and the pride of building something with your own two hands.
Well, buckle up, because you've come to the right place. This is your ultimate guide to designing and building your dream 10x12 garden shed.
First Things First: The Foundation
Imagine building a house on a shaky, uneven surface. Doesn't sound like a good idea, right? Same goes for your shed. A solid foundation is crucial for stability and longevity.
Concrete Slab: The most durable option, but also the most labor-intensive. You'll need to pour a concrete pad, which requires some serious preparation and tools. However, it's the best choice for longevity and resisting moisture.
Wooden Skirts: A simpler and cheaper alternative. Wooden skirts sit directly on compacted gravel, providing a raised platform for your shed. Be mindful of moisture issues, especially if you're in a humid climate.
Pressure-Treated Timber: A good compromise between durability and ease of installation. Pressure-treated lumber is resistant to rot and decay, making it a great option for contact with the ground.
Framing: The Bones of Your Shed
The framing is the structural backbone of your shed. It's what gives it its shape and strength.
Choose Your Wood: For most sheds, 2x4s are a common choice. But, depending on your location, you might want to go with pressure-treated lumber for the bottom plates.
Plan for the Walls: You'll need studs, top plates, and bottom plates. Don't forget the bracing! This will add strength to your walls and prevent them from bowing or warping.
Build the Roof: The roof is a crucial element. Decide whether you want a gable roof (classic and easy), a shed roof (simpler design), or something more adventurous.
Siding: The Skin of Your Shed
Now, it's time to give your shed some personality. This is where you can let your creativity shine.
Wood Siding: Classic and timeless. Cedar, pine, and redwood are popular choices, but don't forget about reclaimed wood! You can even stain or paint it to your liking.
Vinyl Siding: Low-maintenance and durable, comes in a variety of colors and styles. A great option if you're looking for something easy to care for.
Metal Siding: Another low-maintenance option, often made of corrugated steel or aluminum. It offers good protection from the elements and can even be recycled!
Roofing: Keeping It All Covered
Your roof is the final frontier of your shed. It's what keeps you dry and your belongings safe.
Shingles: Asphalt shingles are a popular choice, but you can also go for more premium options like cedar shakes or metal roofing.
Tar Paper: A layer of tar paper between the roof decking and shingles helps prevent leaks and adds extra protection.
Ventilation: Don't forget about ventilation! Adding vents to your roof will help prevent moisture buildup and keep your shed airy.
Doors and Windows: Letting the Light In (And Out)
Choosing the right doors and windows is all about function and style.
Doors: Double doors are great for easy access, while a single door can be a more compact option. Think about the size and style you need.
Windows: Adding a window can bring in natural light and create a more airy feel. Consider the size, shape, and placement of your windows.
Adding the Extras: Bells and Whistles
Once you have the basics down, it's time to add some personal touches.
Flooring: A simple concrete floor is functional, but you can always add a layer of wood or tile for a more polished look.
Shelving: Plenty of shelving is a must! It'll keep your tools and supplies organized and easy to find.
Workbench: A workbench is a great addition if you plan to use your shed for crafts or woodworking.
Electrical Outlets: If you want to use power tools or even just charge your phone in the shed, consider adding electrical outlets.
Let's Get Down to Business
Once you've got your design plan in place, it's time to get your hands dirty.
Gather Your Materials: Make a list of everything you'll need, including wood, siding, roofing, windows, doors, and hardware.
Gather Your Tools: You'll need a basic set of carpentry tools, including a hammer, saw, drill, level, tape measure, and screwdriver.
Start Building: Refer to building plans or tutorials to guide you through the construction process. Take your time and enjoy the process.
Building Your Dream Shed: A Labor of Love
Building your own 10x12 garden shed is a rewarding project that will provide you with a functional and personalized space for years to come. So get out there, get your hands dirty, and start building your dream!
Remember, this is your project, your vision. Don't be afraid to experiment, customize, and make it truly your own. Enjoy the journey, and congratulations on embarking on this exciting adventure!
The cheapest 8x12 shed plans for a budget-friendly build
Alright, so you're dreaming of a shed. Maybe you need extra storage, a workspace, or just a cozy little retreat. But let's face it, building costs can be a real buzzkill. Don't worry, my friend! You don't have to break the bank to build your own 8x12 shed. With a bit of planning, some elbow grease, and these budget-friendly plans, you can have your dream shed without the dream-crushing price tag.
### 1. Embrace the Power of Free (and Almost Free) Resources
Let's start with the basics: those plans. The internet is your oyster when it comes to free shed plans. Sites like [Insert some popular free shed plan websites here] offer a range of plans, some even specifically for an 8x12 shed. A quick Google search will also unearth countless free plans and even detailed guides.
But why stop at free? Check out your local library or community center. They might have books on shed construction, or maybe even a lending library of tools! You can also find used building supplies like lumber at bargain prices at [Insert websites for used building materials, e.g., Craigslist, Facebook Marketplace, etc.].
Tip: Don't be afraid to ask! Local lumberyards or construction companies might have leftover scraps you can snag for cheap, or even offer some advice from the pros.
### 2. Choose Your Building Materials Wisely
Now let's talk about the building blocks of your shed: the materials. The key here is to choose smart, budget-friendly options.
Lumber: Pressure-treated lumber is essential for the foundation and bottom plates to prevent rot, but for the rest of the frame, you can get away with regular framing lumber. Consider using pine or spruce, which are often more affordable than other woods like fir. Check for discounts on dimensional lumber, which are often available in bulk.
Roofing: Shingles are a classic choice, but for a truly budget-friendly option, consider using corrugated metal or even recycled plastic roofing. These options might not be the fanciest, but they'll do the job and save you money.
Siding: You can go with traditional wood siding, but look for affordable options like vinyl or fiber cement siding. These materials are durable, easy to install, and often come in a variety of colors.
Pro Tip: Before you head out to buy lumber, create a detailed materials list. This will prevent you from overspending or buying unnecessary items. And don't be afraid to haggle! You might be surprised how willing sellers are to negotiate.
### 3. Embrace DIY (and Enlist Some Help)
Okay, so you've got your plans and materials, now it's time to get your hands dirty. Building your own shed might seem daunting, but trust me, it's a rewarding experience! And with a little bit of DIY, you'll save a ton of money. You'll need some basic construction skills, but there are plenty of resources online and at your local library to help you learn the ropes.
But you don't have to go solo! Enlist the help of friends or family, especially if you're not a seasoned builder. Two pairs of hands are always better than one, and you'll have more fun building together. Remember, it's a team effort, and everyone can contribute their skills (even if it's just holding a piece of lumber steady).
Tip: If you need some heavier equipment like a saw or drill, consider renting them instead of buying them. This will save you money in the long run, especially if you don't plan on using them regularly.
### 4. Prioritize Functionality Over Frills
Remember, this is a shed, not a mansion. Focus on practicality over fancy features. You don't need a fancy door, a skylight, or multiple windows. Keep it simple, and you'll save money on materials and installation.
Doors: A single, sturdy door is all you need. Look for used doors at salvage yards or online marketplaces. You can even repurpose an old barn door for a unique and budget-friendly look.
Windows: A few small windows for ventilation are sufficient. You can find simple, inexpensive windows at most home improvement stores.
Finishing touches: Skip the fancy trim work and painting. A simple stain or sealant will protect the wood and give your shed a natural look.
Pro Tip: Consider adding a simple shelf system instead of building permanent shelves. This will give you flexibility to adjust the storage layout as needed.
### 5. Embrace the Unexpected (and the Savings!)
Building a shed is an adventure. There will be unforeseen challenges and last-minute adjustments. Embrace these moments as learning opportunities, and don't be afraid to get creative with your solutions. You might find a cheaper alternative to a specific material, or a clever way to repurpose something you already have.
Recycling and repurposing: Look for ways to reuse or repurpose materials. Old pallets can become shelves or decorative elements. Wine barrels can be turned into planters or seating. Get creative and find unexpected uses for items you might have tossed aside.
Thinking outside the box: Sometimes, a simple tweak in the design can save you a lot of money. Consider using a smaller foundation or opting for a simpler roof design. Every little adjustment can make a difference.
Tip: Don't be afraid to experiment and ask for help. The construction process might be a little more challenging, but the satisfaction of building something yourself, especially on a budget, is priceless!
### The Budget-Friendly Shed: Your Haven on a Dime
Building a shed doesn't have to be a financial burden. With a bit of research, planning, and DIY spirit, you can create a functional, cozy space that fits your budget. Don't be afraid to get creative, embrace the process, and most importantly, have fun! Remember, it's your shed, your space, and your own personal haven built with your own two hands. Now go out there and build your dream shed, one affordable step at a time!
Step-by-step guide to building a cost-effective pole shed

Alright, you're ready to ditch that cluttered garage or finally have a dedicated space for your hobbies. A pole barn, also known as a post-frame building, is a fantastic solution, especially if you're looking for a cost-effective option. Let's dive in and break down the process, from planning to finishing touches.
1. Dream Big (Then Get Real!)
First things first, let's talk about your vision. What will this pole barn be used for? Storage? Workshop? Garage? Knowing the purpose helps determine its size, layout, and even the type of doors you'll need. Do you have specific equipment or vehicles you need to fit? Think about the future, too â" will your needs change over time?
2. The Foundation: Your Building's Backbone
Pole barns are known for their simplicity, and the foundation is no exception. You'll have several options, each with its own pros and cons:
Concrete Piers: These are sturdy and long-lasting. You'll dig holes, pour concrete, and then set your posts directly onto the concrete. They're perfect for heavier loads and areas with frost heave.
Concrete Slabs: A full concrete slab is great for a finished floor, offering a smooth and level surface. However, it can be more expensive and time-consuming to install.
Wood Posts: This is the most affordable option. You'll need to set them in a gravel bed to ensure stability and drainage. This is best for lighter loads and areas without extreme weather.
3. Choose Your Lumber Wisely:
The posts that hold up your pole barn are crucial. The most common choices are treated lumber (pressure-treated pine or cedar) or steel posts.
Treated Lumber: It's affordable and readily available, but requires proper maintenance and can be prone to rot over time.
Steel Posts: These are incredibly durable, long-lasting, and resistant to pests and rot. They're a bit more expensive upfront but can be a good investment in the long run.
4. Roofing: Protecting Your Investment
Now, let's get to the roof. Consider the following:
Pitch: A steeper roof helps with snow and water runoff, but can also add to the cost of framing.
Material: Metal roofing is popular for its durability, affordability, and low maintenance. Asphalt shingles are another option but require more upkeep.
Insulation: If you plan to use the barn for storage, consider insulating it, especially in colder climates. This will help regulate temperature and reduce heating/cooling costs.
5. Framing: The Skeleton of Your Building
Once your posts are set, you'll need to frame the walls and roof. This involves installing horizontal beams and rafters, and it's crucial for structural integrity.
Wood Framing: This is a traditional method and relatively affordable. Choose high-quality, treated lumber for durability.
Metal Framing: This option offers strength, fire resistance, and minimal maintenance. It's slightly more expensive than wood framing.
6. Siding: Making it Look Good (and Last)
The siding provides the exterior finish of your pole barn. You'll find a wide variety of materials, from affordable options like vinyl and corrugated metal to more premium choices like wood siding and fiber cement.
Corrugated Metal: It's durable, weather-resistant, and affordable. It comes in various colors and finishes.
Vinyl Siding: This is low maintenance, easy to install, and comes in various colors and textures.
Wood Siding: Offers a classic look but requires more upkeep and is typically more expensive.
7. Doors: A Key to Your Building
The doors are the gateway to your pole barn, so make sure they fit your needs. Consider:
Garage Doors: Great for vehicles and large items. They come in different sizes and styles.
Sliding Doors: A good choice for large openings. They can be manually operated or automated.
Double Doors: Offer easy access for larger equipment or heavy items.
8. Windows: Adding Light and Air
Windows can brighten up your pole barn and improve ventilation. You can choose from a variety of styles, including sliding windows, casement windows, and fixed windows.
9. Finishing Touches: Adding Functionality
Now that you've got the basics down, you can add functional and aesthetic finishing touches:
Flooring: Concrete is a common choice for pole barns, but you can also opt for gravel, wood, or even epoxy flooring.
Electrical: Plan your lighting and outlet placement to accommodate your specific needs.
Painting: Give your barn a fresh look with a coat of paint. Choose a durable and weather-resistant paint.
10. Do It Yourself or Hire It Out?
The decision to build a pole barn yourself or hire a contractor comes down to your skills, experience, and time constraints.
DIY: It's a cost-effective option, but requires time, effort, and a good understanding of construction.
Hiring a Contractor: Offers convenience and professional expertise. However, be sure to get detailed quotes and compare prices.
11. Permits and Inspections:
Before starting construction, be sure to check your local building codes and obtain any necessary permits. This will ensure your project meets safety standards and complies with regulations.
Building a pole barn is a rewarding project. By following this guide, you can create a durable and functional space that meets your needs and fits your budget. Remember, planning, patience, and a bit of DIY spirit can get you a fantastic pole barn!
How to save money by building your 8x10 shed yourself

So, youâve got a pile of stuff that's threatening to take over your garage, your basement looks like a jungle gym for spiders, and your garden tools are crying out for a proper home. Sounds familiar? Well, you know what they say â" âwhen life hands you lemons, build a shed!â
And let's be honest, buying a pre-made shed can feel like a punch in the wallet. But fret not, my friend! You can build your own 8x10 shed for a fraction of the cost. Not only will it give you that sense of accomplishment, but you'll also be learning a new skill (or two) along the way. Think of it as a DIY adventure, a journey to a more organized you!
Step 1: The Planning Stage - It's Not Just About Nail Guns and Wood
Before you even start thinking about lumber and nails, you need to plan your attack! This step is crucial, and it's way more exciting than it sounds.
Location, Location, Location: First things first â" whereâs this shed going to live? Make sure itâs on level ground, with enough space around it for you to work comfortably. Also, check for any pesky utility lines that might be in the way.
The Blueprint: A Shed of Your Dreams: Now for the fun part â" deciding what your shed will be like! Do you need a window for light, a door big enough for your lawnmower, or maybe even a workbench? Sketch it out, measure everything, and donât be afraid to get creative. There are tons of free shed plans online that you can customize to your heartâs content.
The Budget Breakdown: Keeping It Real: Don't jump into buying every fancy material out there. Make a realistic budget. Research prices for lumber, roofing, siding, and other materials. Consider what you can do yourself and what you might need to hire someone for (like digging a foundation).
Building Codes and Permits: Just the Facts: Always check your local building codes and see if you need a permit. Trust me, you don't want to find yourself in the middle of construction with a grumpy inspector knocking on your door.
Step 2: Gather Your Arsenal â" The Tools of the Trade
Now that youâve got the plan, it's time to get your tools ready. Here are some essentials:
The Power Trio: A circular saw, a drill, and a jigsaw. These are the core players for cutting, drilling, and making those fancy shapes.
Measure Twice, Cut Once: A measuring tape, a level, a speed square, and a pencil will keep your cuts precise and your walls plumb.
Putting It Together: A hammer, a nail gun (if you're feeling ambitious), and a set of screwdrivers are your best friends for assembling your shed.
Safety First: Don't forget safety gear! Eye protection, gloves, and a good pair of work boots will keep you protected from flying debris and potential hazards.
Step 3: Laying the Foundation â" The Bedrock of Your Shed
Building a strong foundation is non-negotiable. It's like the base of a cake â" if it's not solid, the whole thing will crumble.
Concrete Block Foundation: This is a classic and sturdy option, especially if you're planning on putting a heavier shed on it.
Wooden Foundation: For smaller sheds and lighter loads, a wooden foundation can be easier to build. Just make sure to use pressure-treated lumber to resist rot and decay.
Pier Foundation: This is a good choice if your soil is uneven. Concrete piers are placed at strategic points to support the shed.
Step 4: Framing â" The Skeleton of Your Shed
Now comes the fun part â" building the framework! It's like putting together a giant puzzle, but with nails and wood.
Floor Joists: Start with the floor joists, which will form the base of your shed floor. Make sure to space them correctly for support.
Wall Studs: Next, erect the walls using vertical studs. Space them according to your local building codes for stability and insulation.
Roof Framing: Finally, build the roof frame with rafters and supporting beams. Choose the right roof pitch based on your local climate and snow load.
Step 5: Sheathing and Siding â" Covering Up Your Creation
Once the framing is done, it's time to add the layers that will make your shed look good and function properly.
Sheathing: Plywood or OSB (oriented strand board) is used to cover the exterior walls and roof for strength and a smooth surface for siding.
Siding: There are tons of siding options â" wood, vinyl, metal, or even composite. Choose what works best for your budget and style.
Roofing: Again, plenty of options â" asphalt shingles, metal roofing, or even cedar shake for a rustic look. Think about your climate and budget when choosing.
Step 6: Windows and Doors â" Adding Character and Functionality
Now it's time to give your shed some personality and functionality.
Window Options: Windows let in light and make your shed feel more inviting. Choose the size and style that best suits your needs.
Door Selection: A sturdy door is essential for accessing your shed. Consider the size and style based on what you'll be storing inside.
Step 7: Finishing Touches â" Making Your Shed Shine
Almost there! It's time to add the finishing touches that will make your shed truly stand out.
Paint or Stain: Give your shed a fresh coat of paint or stain to protect the wood and add some personality. Choose colors that complement your home or your landscape.
Insulation and Electrical: If you plan on using your shed for more than just storage, consider adding insulation to keep it warm or cool. You might also want to install electrical wiring for lights or appliances.
Step 8: The Big Reveal â" Moving Day!
Finally, you've reached the grand finale! Your DIY shed is ready for its big reveal.
Clean Up and Organize: Give your shed a good sweep and organize your belongings before moving them in.
Celebrate Your Achievement: Take a moment to admire your hard work! Building your own shed is a major accomplishment, and it's a testament to your DIY spirit.
Cost Savings and Benefits:
Building your own shed offers huge cost savings compared to buying a pre-made one. You can control the quality of materials and build it exactly to your specifications. Plus, you gain valuable skills and a sense of pride knowing you built it yourself.
Challenges and Considerations:
Building a shed is not without its challenges. You'll need patience, determination, and maybe a few extra hands to help with lifting and carrying heavy materials. Be prepared to learn as you go and don't be afraid to ask for help when needed.
Tips for Success:
Plan ahead: Careful planning is essential to avoid mistakes and delays.
Research and learn: Don't be afraid to seek guidance from experts or online resources.
Take breaks: Don't try to do everything at once. Take breaks to avoid burnout.
Have fun! Building a shed is a rewarding experience. Enjoy the process!
So, there you have it! With a little planning, determination, and maybe a bit of sweat equity, you can build your own 8x10 shed and save a bundle of money. It's a project that will give you a sense of accomplishment and a dedicated space for all your belongings. Get out there, grab your tools, and start building your own shed today! Happy building!